Manufacturing Menu: Enhance Your Business with Streamlined Processes
Last edited on Aug, 22 2024 12:44:33 PM
Reading time: 6 minutes
Written by Chelsea Delich
Table of contents
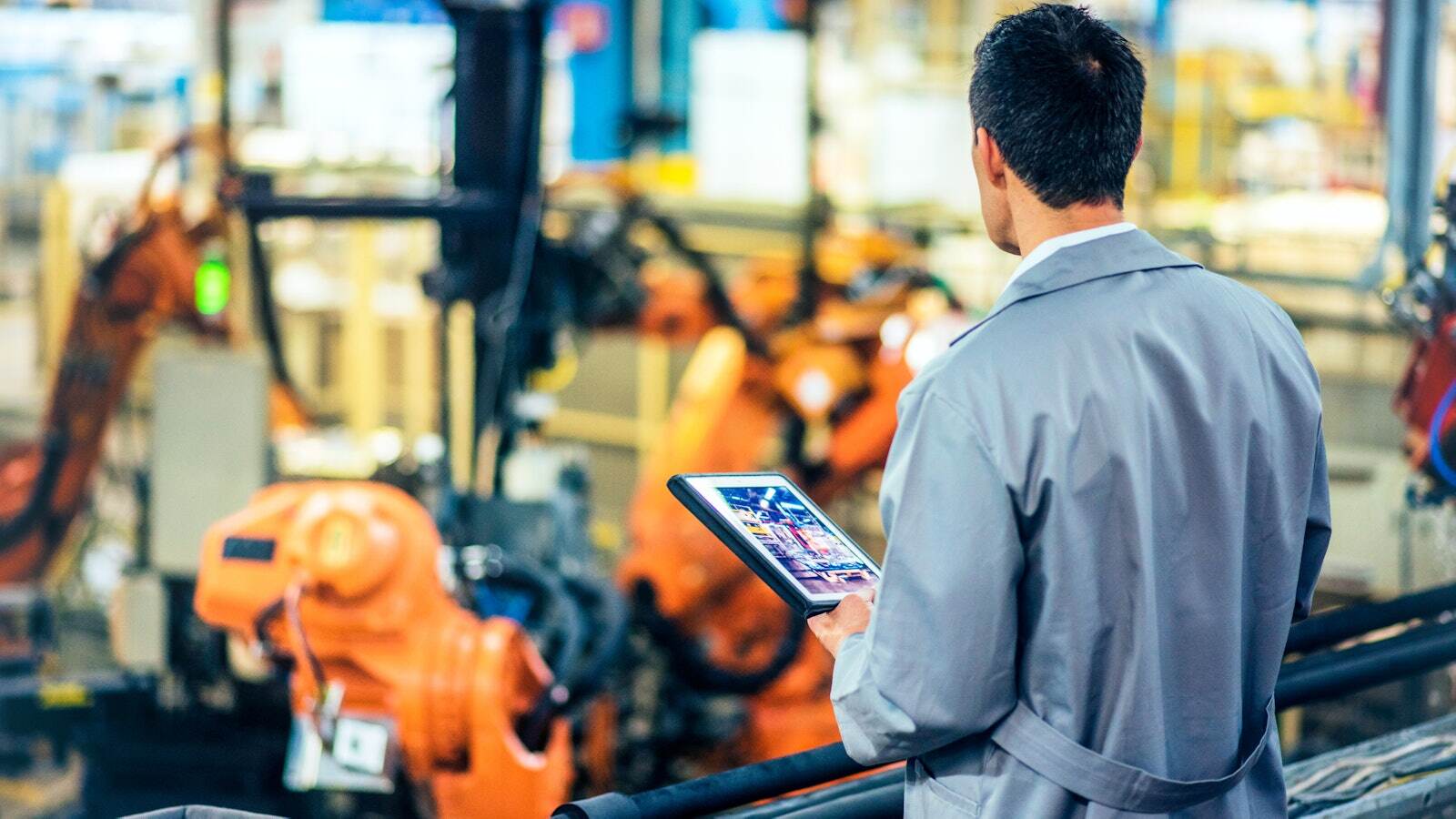
While manufacturing companies are primarily focused on production, they can only execute their core tasks thanks to a diverse set of supporting processes. Consider, for example, visitor registration, reserving the right rooms for meetings, enriching data and processing returns or repairs correctly.
Modern facility management goes beyond simple activities such as keeping a workplace clean or monitoring a parking lot. It includes and promotes all activities carried out within an organization and focuses on managing and controlling the support activities for the primary process. Especially within large companies, managing all supporting processes can be a complex task. That is why this is a fixed component in the Manufacturing Menu
About the Manufacturing Menu
The Manufacturing Menu focuses on all production phases and domains within manufacturing companies, with attention to specific challenges. It provides practical solutions to promote agility, innovation and adaptability through Mendix's low-code. In this article we take a closer look at the challenges surrounding facility management and learn how to streamline and optimize support processes with the right applications.
This blog is part of the series: "Manufacturing Menu: Practical Solutions for the Manufacturing Industry" If you are also interested in getting the most out of human capital with modern HR tools, we invite you to read this blog as well. Discover more here.
Why Supporting Processes are Essential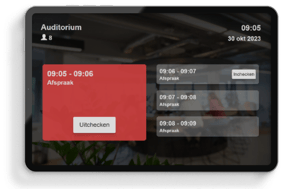
Supporting processes play a crucial role in the operations of modern manufacturing companies. They are not a burdensome cost, but are necessary to achieve the key business objectives both strategically and operationally. Effective facility management adds value to your organization and ensures that office staff and those on the production floor can work in a suitable environment equipped with all necessary facilities ('fit for use').
Effectively managing supporting processes begins with insight and efficiency, two areas where many manufacturing companies fall short. Manual workflows still dominate, creating room for errors and unnecessarily consuming time and effort in supporting processes. Fortunately, the right IT tools and applications provide a solution. For example, tools such as the Emixa Room Tablet application streamline processes such as meeting room reservations, ensuring optimal use of facilities and helping teams collaborate more effectively. With these tools, you can turn support processes into value-added assets that help you get more out of your core business. Read on to discover some inspiring real-world examples.
Room Reservations Have Never Been Easier
A Dutch transportation company, faced difficulties in reserving rooms for meetings, presentations and conferences. It was often unclear if certain rooms had been reserved, leading to practical and facility-related issues. For example, inefficient use of space due to regular "no-show reservations" (a room is reserved, but ultimately no one shows up) or people and groups having to vacate a room due to double bookings or cancellations.
To tackle this problem thoroughly, Emixa developed a special application for room reservations. Each room now has its own tablet that displays detailed and accurate information about that room or hall (size, availability, reservations, facilities). Booking a meeting room is now simple and lightning-fast with just two mouse clicks. The application is integrated with Outlook and allows reservations to be automatically cancelled if organizers and participants fail to check in by a certain time. The space then becomes available again for other groups and individuals.
The reservation app proves its value in several ways. People can see at a glance whether meeting rooms are available or not, saving a lot of time when booking. Those minutes can now be invested in productive meetings and discussions that propel the company and work forward. The application also ensures that the transportation company uses its meeting rooms much more efficiently and gains insight into valuable aspects such as the popularity of specific rooms, no-shows and the number of quick reservations.
Customer Case Stichd - Top Level Data Enrichment
For Stichd, a company specializing in fashion essentials, fanwear and sports clothing, Emixa developed an application that takes data enrichment to a higher level. The company transitioned from Navision to SAP and found that some essential modules were missing in the new setup. To bypass this system limitation and work effectively, the clothing manufacturer needed additional fields. Additionally, the company still relied heavily on Excel, leading to labor-intensive and error-prone processes because each process required many manual actions by a large number of people.
The new application creates new modules for data enrichment and supports SAP. One module, for example, focuses on accurately comparing different shippers, while another module provides for the creation of automated and error-free workflows for clothing requests. The result? Workflows are no longer based on error-prone manual work, but are faster and much more accurate. Additionally, the clothing company no longer uses different, poorly integrated systems. Instead, there is now one SAP system and the gaps in the system are filled using advanced Mendix technology.
Customer Case - Rent Cars Without Worries
For VDL Nedcar, a leading Dutch car manufacturer, we developed the car rental app. Previously, the rental process largely relied on Excel sheets. The complexity and error-proneness of the old system often meant there was no insight into the availability of cars and any damage. The result? The company had to rent cars from an external party, incurring significant additional costs.
The car rental app requires renters to provide a photo of the car both upon receipt and return, and to fill out a report in case of damage. Additionally, the application allows for automatically selecting a car based on desired specifications and the expected number of passengers. Thanks to the app, the car company now knows which car is available on which days. Additionally, there is a much better and more accurate insight into damages.
Want to Improve your Supporting Processes?
Facilities and supporting processes are vital in the manufacturing, enabling focus on core tasks and contributing to operational and strategic goals. Looking to enhance your supporting processes and facility management? Curious about how we leverage our knowledge of low-code, Mendix, digital twinning, plant simulation, and Siemens technology can help you with this? Feel free to contact us to explore the possibilities.
Explore the Manufacturing Blog Series
This blog is part of the Manufacturing Menu blog series, which you can view here:
- The Manufacturing Menu
- From Product Design to Services
- Supplier Management
- Warehousing & Logistics
- Marketing & Sales
- Safety, Health & Environment
- Quality
- Utilization & Performance
- Finance, Control & Reporting
- HR
- IT, Data & Facilities
Last edited on Aug, 22 2024 12:44:33 PM
Reading time: 6 minutes
Written by Chelsea Delich
Also see..
OverviewManufacturing Menu: A Strong Foundation for the Perfect Product
Before a product reaches the market, a manufacturing company must go through various preparatory...
Read more ⟶Manufacturing Menu: The Power of Quality Management and Compliance
In the fast-paced world of manufacturing, ensuring world-class quality isn't just a nice to have -...
Read more ⟶Manufacturing Menu: Smart Solutions for Future Warehouse Management
In the dynamic world of logistics and warehouse management, companies face the challenge of...
Read more ⟶