What is a Manufacturing Menu—and Why Is It the Secret to Building Better Products?
Last edited on Jul, 01 2025 10:51:27 AM
Reading time: 6 minutes
Written by Minke van Dooremalen | Marketing Manager
Table of contents
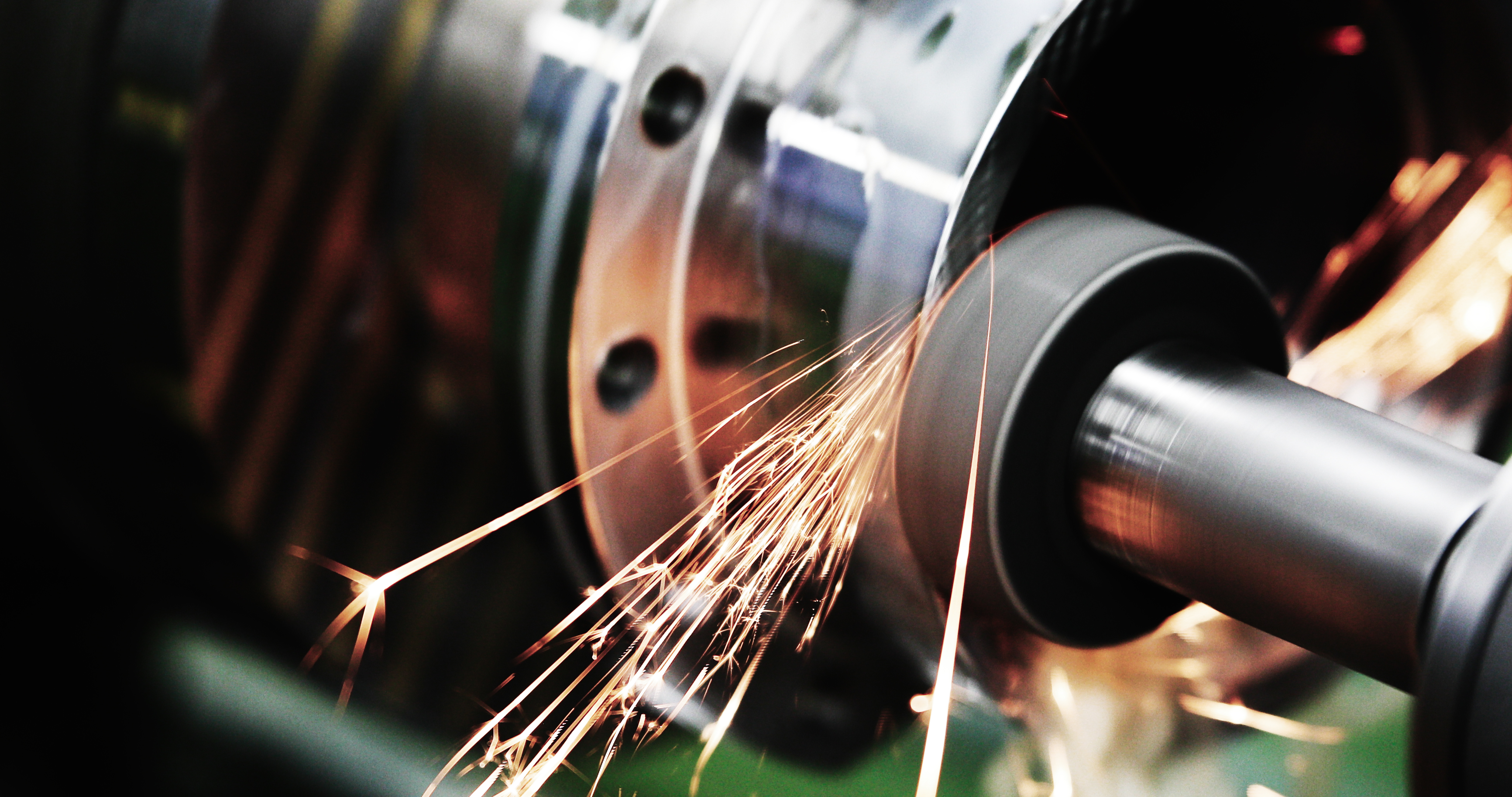
In today’s complex production environments, product success doesn’t just depend on design innovation or customer demand—it starts with the right manufacturing foundation. That’s where a manufacturing menu comes into play. It’s not a culinary term, but a critical structure that ensures every product is built efficiently, consistently, and at the highest possible quality. At Emixa, we help manufacturers standardise and digitise this process using Siemens’ advanced platforms like Teamcenter and Opcenter
What is a Manufacturing Menu?
A manufacturing menu is a structured, standardised definition of all the steps, materials, machines, and resources required to manufacture a product. Think of it as a digital recipe that connects engineering, planning, and production in one unified model.
Unlike traditional spreadsheets or disconnected documents, a manufacturing menu lives within an integrated digital environment—ensuring that every department operates from a single source of truth. This reduces miscommunication, improves traceability, and speeds up production planning.
Who benefits from using a manufacturing menu?
Nearly every stakeholder in the product lifecycle benefits:
- Product Engineers: Ensure designs are manufacturable and linked to approved processes
- Production Planners: Streamline routing, resource allocation, and scheduling
- Operators: Access clear, standardised instructions and work packages
- Quality Teams: Track compliance and deviation from baseline
- Supply Chain Managers: Align procurement to actual production needs
At Emixa, we see the biggest value delivered in high-variation, high-complexity manufacturing environments where precision and repeatability are crucial.
When should a business implement a manufacturing menu?
If your company is:
- Scaling up production lines or product variants
- Experiencing quality issues due to inconsistent build instructions
- Relying on tribal knowledge or outdated paper-based work orders
- Struggling with disconnected systems between design and production
- Launching smart factory or Industry 4.0 initiatives
… then a digital manufacturing menu is essential. It enables seamless coordination between design, engineering, and manufacturing.
Where does a manufacturing menu fit in the digital thread?
A manufacturing menu forms the bridge between Product Lifecycle Management (PLM) and Manufacturing Execution Systems (MES). It transforms engineering data into structured, executable manufacturing content.
The digital thread flow:
- Design and BOM in Teamcenter
- Process planning and work instructions
- Routing and scheduling in Opcenter Execution
- Live execution and feedback on the shopfloor
- Closed-loop improvement through analytics
Why is a manufacturing menu better than traditional production planning?
Legacy methods like Excel or printed process sheets introduce risk, including:
- Manual errors in work instructions
- Lack of version control or revision tracking
- Inflexibility in adapting to product changes
- Limited visibility across global production teams
With a digital manufacturing menu, companies gain:
- Automates versioning and approvals
- Integrated quality and compliance tracking
- Faster product ramp-up and change implementation
- Real-time shopfloor updates and analytics
What does success look like with a digital manufacturing menu?
Manufacturers who implement this structure experience:
- Fewer errors and delays during product launches
- Improved production agility and resource utilisation
- Better communication between engineering and operations
- Increased traceability and compliance
- Faster response to customer-specific requirements or design changes
At Emixa, we help clients integrate Siemens Xcelerator tools to build a digital foundation that supports scalable, sustainable production—driven by clarity and control.
Conclusion
A manufacturing menu is more than a set of instructions—it’s the digital blueprint for operational excellence. When built on robust platforms like Teamcenter and Opcenter, it ensures that the path from concept to finished product is clear, standardised, and agile.
Whether you're improving first-time-right production or scaling globally, Emixa can help you lay the digital foundation for the perfect product—every time.
Last edited on Jul, 01 2025 10:51:27 AM
Reading time: 6 minutes
Written by Minke van Dooremalen | Marketing Manager
Also see..
OverviewWhat is LEAN Manufacturing?
Lean manufacturing, also known as lean production, is a method of making production processes more...
Read more ⟶What is Overall Equipment Effectiveness (OEE)?
In the world of manufacturing, performance matters. Businesses are under pressure to produce more,...
Read more ⟶Manufacturing Menu: Master Cash Flow with Financial Management
Although manufacturing companies are primarily producers, good financial management (invoicing,...
Read more ⟶