Do Machine Factories Risk Becoming Redundant?
Last edited on Aug, 08 2025 03:24:09 PM
Reading time: 6 minutes
Written by Bart Stuve
Table of contents
Share article
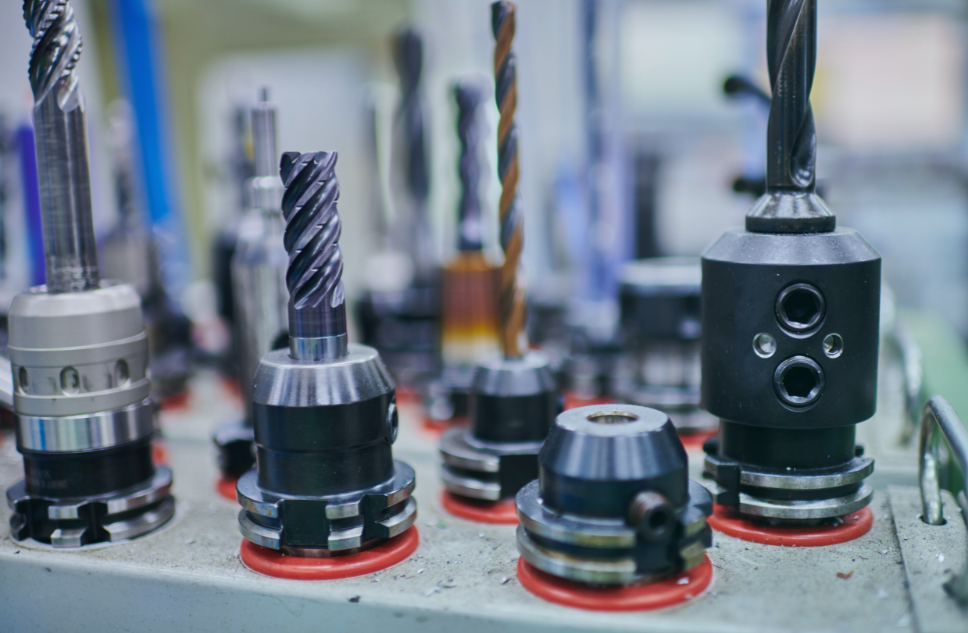
Blackberry, Blockbuster and Kodak. History is filled with companies that were once leaders in their own industries, but were eventually overtaken by competitors or even ceased to exist entirely. The common thread in their downfall? They failed to adapt to the fundamental shift in expectations from the market and demand from the customer, driven by competitors who made use of the latest technology.
Blackberry, a pioneer in mobile phones, confidently optimised the QWERTY keyboard and scroll wheel. Meanwhile, Apple conquered market share with an innovative touchscreen and mobile operating system. Blockbuster, the company where you could rent films in physical stores, did not adapt itself in time to the changing business models and new technological possibilities that Netflix did take advantage of. Kodak, the pioneer of digital photography, hesitated to move away from traditional film activities, allowing competitors like Sony, Nikon, and Canon to seize the opportunity and advance the invention.
The mentioned companies faced challenges in the initial years of digitisation, a trend that has now permeated almost all industries, reshaping both products and production processes. Presently, leading organisations are actively refining their digitalisation strategies, considering how products and services are developed, produced, and enhanced.
Both large and small manufacturers must adapt
The latest wave of technologies, Industry 4.0, gives a new meaning to service, competition and customer expectations across the entire Supply Chain. From small businesses to industry leaders.
Industry 4.0 makes it possible to integrate digital technologies into all business processes, creating an 'End-to-End Platform' that seamlessly connects the virtual and physical worlds. Digital twins, virtual representations of products and production processes, are connected via a digital thread: An always available, accessible feed of real-time data. This digital thread is available to everyone at any time and allows product and production engineers to work simultaneously because they have immediate access to the information they need.
Industry 4.0 transforms modern machine factories no less than new technologies transformed the mobile phone, film distribution or photography industries. However, recent research suggests that many machine factories are not well prepared for this. Of the machine factories surveyed:
- Over 50% still rely on standalone CAD and CAM systems
- Less than 30% manage and control their data
- Around 75% rely on disjointed CMM systems
- 61% still use paper documentation
- Only 37% use 3D printing in production
The virtual Supply Chain is about businesses, not technology
Too many machine factory owners believe that strategies that helped them in the past will also bring success in the future. Expertise in production was the competitive advantage for many machine factories, but expertise alone is no longer enough these days. As essential parts of an increasingly global supply chain, machine factories must shift their traditional focus to a customer-focused one, producing products faster and better than ever before, where and when the customer wants.
A digitisation strategy is not just about showcasing new technologies, although it is often presented that way. Digitisation is about a robust business strategy, aiming to lead a successful production operation.
Machine factories that apply Industry 4.0 technologies are better prepared to:
- Secure orders globally by delivering high-quality products faster, outpacing competitors.
- Increase margins through investments in new processes rather than tinkering with outdated ones.
- Enter new markets with a focus on innovation and growth.
- Embrace new manufacturing technologies such as Additive Manufacturing, advanced robotics and automation, and emerging technologies like Artificial Intelligence and Virtual Reality.
It is important to note that Blackberry, Blockbuster and Kodak did not fail because they did not realise how new technologies were transforming their industry, or because they did not adapt. They failed because their response was not aligned with the challenge.
An article in the Harvard Business Review, "Why Good Companies Go Bad," explains:
"Managers of endangered companies typically identify the threat early, thoroughly analyse its implications for their business, and initiate a flurry of initiatives in response. However, despite these efforts, the companies continue to struggle."
“The problem is not an inability to take action, but an inability to take appropriate action.”
Incremental technological advancements merely address issues from the past decade, failing to tackle fragmented processes and disconnected data across design, engineering, production, and quality.
Explore options step-by-step
Machine factory owners often perceive Industry 4.0 as beyond their reach. It is deemed too expensive, time-consuming, and disruptive to ongoing operations. Yet, it's feasible to embark on a gradual journey towards Industry 4.0 transformation. At Cards, we assist companies with a well-crafted strategy and planned implementation that considers immediate ROI and integration with existing business processes while accelerating organizations on the path to digitalisation.
Bottom Line
Machine factories confront new challenges shaped by evolving market expectations. Customers no longer tolerate errors or delays, and demand responsiveness beyond the capabilities of inefficient production processes. In response, machine factories must adopt an end-to-end solution; failure to do so risks falling behind the competition. Curious about the benefits of the digital machine factory? Reach out to us, and we'll gladly provide you with more information.
Last edited on Aug, 08 2025 03:24:09 PM
Reading time: 6 minutes
Written by Bart Stuve
Share article
Also see..
OverviewEvent Recap: Revolutionize Manufacturing on November 23, 2023
An Innovative Journey at Siemens: Diving into the Future of Manufacturing!
Read more ⟶Manufacturing Menu: Optimize Resources and Performance with Top Tools
Manufacturing companies operate in a challenging and dynamic marketplace. They face volatile...
Read more ⟶Event Recap: Exploring the Future of Manufacturing, May 22nd 2024
Unveiling the Future if Manufacturing at Siemens Digital Experience Center.
Read more ⟶