Digital Twin & Thread: From Complexity to Competitive Advantage
Last edited on Aug, 08 2025 03:31:25 PM
Reading time: 6 minutes
Written by Bart Stuve
Table of contents
Share article
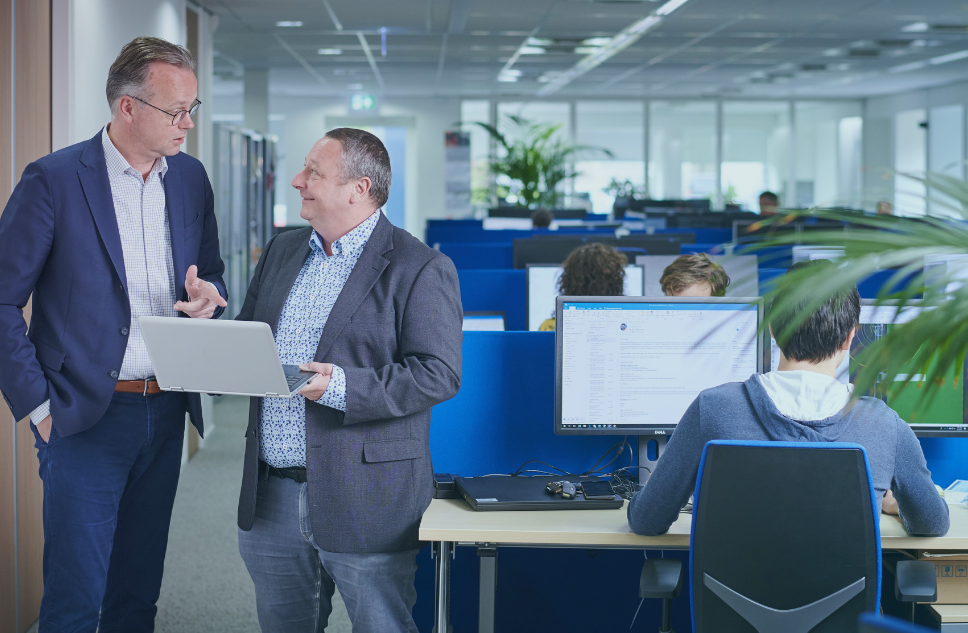
The complexity of contemporary product and production processes is increasing explosively. Companies have to deal with customised products, quality, cost reduction, flexibility, sustainability and so on. Complexity is the central theme for all these topics, but how can you turn this complexity into a competitive advantage?
Most manufacturing companies know that they need to continuously evaluate and improve the product development process to keep up with the competition. To this end, incremental investments are constantly being made that consciously or unconsciously contribute to a total digital transformation. In previous blogs we have discussed various separate topics in the field of digitisation that are relevant for manufacturers.
We have talked about:
- Breaking down the silos between engineering and production
- Gaining insight into production processes via simulation models
- The virtual commissioning of a line or machine
- The transition from 2D drawings to Model Based Definition
- Data exchange within the supply chain
For all the topics above, they contribute to digitisation within manufacturing. Of course, there are many other important technologies or solutions besides these topics that we will explain in future blogs.
This time, our focus is on the overarching theme that ties all these topics together: 'Digital Twins' and the 'Digital Thread.' As we engage with companies about these concepts, we observe a significant increase in manufacturing knowledge over recent years. While only a few years ago, these terms were relatively unfamiliar, it's now apparent that almost everyone has developed their own understanding of them. However, given the varied definitions we frequently encounter, this blog aims to articulate our perspective on these two terms.
Digital Twin
When we talk about digital twins, we often talk about different variants. For example, you can have a digital twin of your product, but also of your production process. In short, a digital twin for me is the digital counterpart of reality, where all relevant up-to-date information is connected. So when we talk about a digital twin of the product, we don't just mean the 3D CAD file. Although this is of course an important part of the digital twin, that file does not contain all the information.
Think of all the requirements and specifications that determine the product, or the performance of the product itself. In our view, a complete digital twin of the product contains simulation models that predict, for example, the rigidity of a product or the air resistance.
Of course, the same applies to the digital twin of production. This also includes all the tools, resources, actions, quality controls, programming, etc. required for actual production. Again, simulation models are included that can predict output, guarantee safety and ergonomics on the floor and prevent bottlenecks or collisions with robots and AGVs.
The added value of these digital twins includes the fact that everything can be validated and prepared in a virtual environment before a physical product or process is set up. This helps companies bring better products to market faster and at lower cost.
Even after the physical products and production processes have been set up, the digital twins offer added value. Most products and processes now contain numerous sensors that collect data on performance. This real-time data can flow back into the digital twins to provide additional insights and implement a process of continuous improvement. However, it is a prerequisite for this that the various applications and departments within companies are well-connected to each other. This brings me to the second term.
Digital Thread
When we talk about the 'Digital Thread' we mean one integrated stream of data across the different phases of the product development cycle. This means both a connection between the different departments within a company, such as sales, engineering, production and service, but also between the different applications within a company, such as CPQ, PLM, ERP, MES, etc.
By connecting all the information, you create a digital thread. This creates traceability in the process. This traceability is becoming increasingly important. Consider the aviation or medical industry, for example. Because traceability ensures that the impact of a change is immediately transparent, and thus prevents mistakes from being made. Does a customer change a requirement halfway through the process? It is then immediately clear which functions and components need to be changed as a result, where they currently are in the process and who is working on them.
Thanks to their predictability and traceability, the Digital Twin and Digital Thread can help companies turn increasing complexity into a competitive advantage.
Up for a brainstorm?
Curious about the other benefits of digital twins and the digital thread? Want to know what digitisation can mean for your business and how we can help you with that? Reach out to us, and we'll gladly provide you with more information.
Last edited on Aug, 08 2025 03:31:25 PM
Reading time: 6 minutes
Written by Bart Stuve
Share article
Also see..
OverviewWhy Companies Need to Be More Ambitious with Their Digital Transformation
Digitalisation Is Not a New Trend
Digitalisation has been an essential part of modern business for...
Read more ⟶The Top 10 Challenges Companies Face in Their Digital Transformation - and How to Deal with Them
Digital transformation is a priority for most established companies. Some have successfully...
Read more ⟶Digital Maturity: How to Turn Your Digital Strategy into Reality
The manufacturing industry is under increasing pressure to operate more efficiently, flexibly and...
Read more ⟶