Collaborating in the Supply Chain: How do you do that?
Last edited on Aug, 12 2025 09:08:53 AM
Reading time: 6 minutes
Written by Bart Stuve
Table of contents
Share article
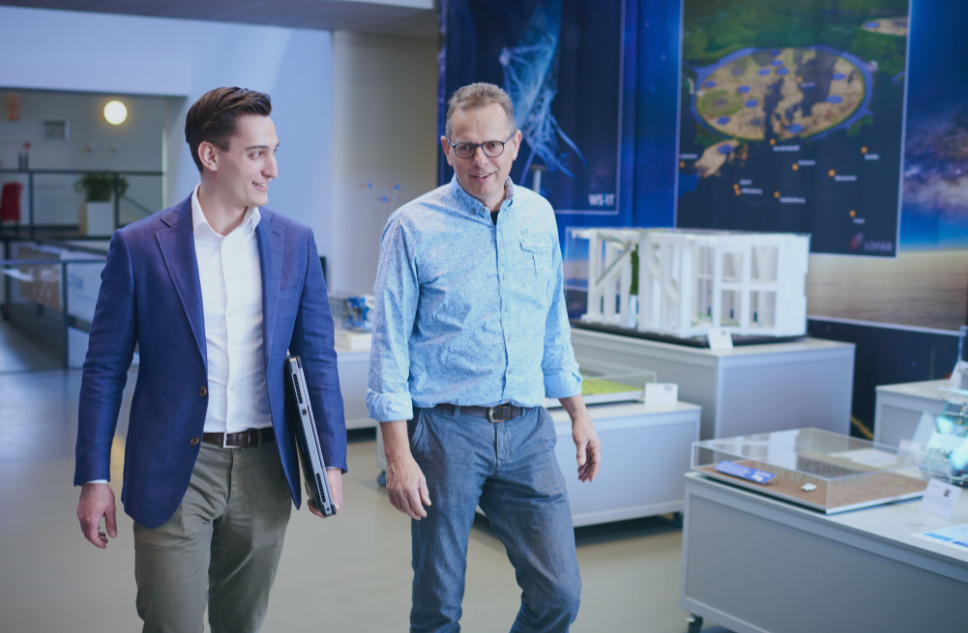
Gone are the days when machine builders exclusively handled in-house development and construction. In the contemporary landscape, most companies either possess their own supply chain with various suppliers or operate as integral components within an Original Equipment Manufacturer's (OEM) supply chain. While this collaboration within Dutch manufacturing companies offers substantial benefits, it also presents significant challenges. How does one manage the critical exchange of data in this intricate web of partnerships?
Every manufacturing entity, irrespective of its industry, feels the increasing pressure of competition, shrinking margins, rising costs and staff shortages. To bring products quickly and seamlessly to market, manufacturers can no longer afford the luxury of time-consuming data exchange, fraught with manual checks susceptible to errors. With increasing product complexity, this problem is only getting bigger and causes more and more challenges.
Firstly, companies have to deal with more and more complex data: assemblies become larger, the number of electronic components increases, there are more specifications and quality checks. In addition, each company has its own way of working and provides data in a different structure. There is a lack of standards. Companies often also lack access to each other's systems. So, how do you ensure data is exchanged securely without exposing yourself to a cyberattack?
Continuous stream of modifications
The challenge often extends beyond a one-time data transfer. During the product development process, continuous modifications arise that need to be implemented properly. Keeping oversight and carefully recording all changes is a time-consuming task that usually has to be carried out by expensive engineers, who should actually be spending their time on completely different tasks.
I still hear too often in the market that this leads to mistakes that only become visible late in the process - and therefore cost a lot of money. This might involve ordering the wrong products, older revisions going into production, increasing lead times with possible penalties from the OEM and a loss of trust in the supplier.
Now what?
We believe that a large part of this problem can be solved by automating and digitising current processes. No more reliance on email and Excel for manual back-and-forth data exchanges! Intelligent data importation is key, where the system can automatically compare data and process changes.
The way you can do this largely depends on the data source. Is your customer's or supplier's data organized in folder structures, and does it arrive consistently at your end? Or do one or both parties have a Product Data Management (PDM) or Product Lifecycle Management (PLM) system where data is securely managed? In the latter case, there are possibilities to use an intermediate portal where data can safely flow from one system to the other.
Regardless of the situation, achieving this necessitates gaining a comprehensive understanding of internal workflows and the modification rules (Change Management). By aligning your customer's or supplier's workflows, you can document this knowledge in templates or rules within a system. Only then can you start to automate.
Get in touch
Information exchange throughout the supply chain is a complex topic. Tackling this issue isn't straightforward, and there can be multiple ways to approach it. Curious about how we can assist you with this? Contact us, and we'll provide you with more details.
Last edited on Aug, 12 2025 09:08:53 AM
Reading time: 6 minutes
Written by Bart Stuve
Share article
Also see..
OverviewThe Top 10 Challenges Companies Face in Their Digital Transformation - and How to Deal with Them
Digital transformation is a priority for most established companies. Some have successfully...
Read more ⟶How Do Trends in the Construction Industry Affect Your Organisation?
The construction industry is evolving rapidly due to technological innovations, sustainability...
Read more ⟶Asset Intelligence Network (AIN) for Data Exchange in the Chain
One of the most important trends within Asset Management concerns increasing the availability of...
Read more ⟶