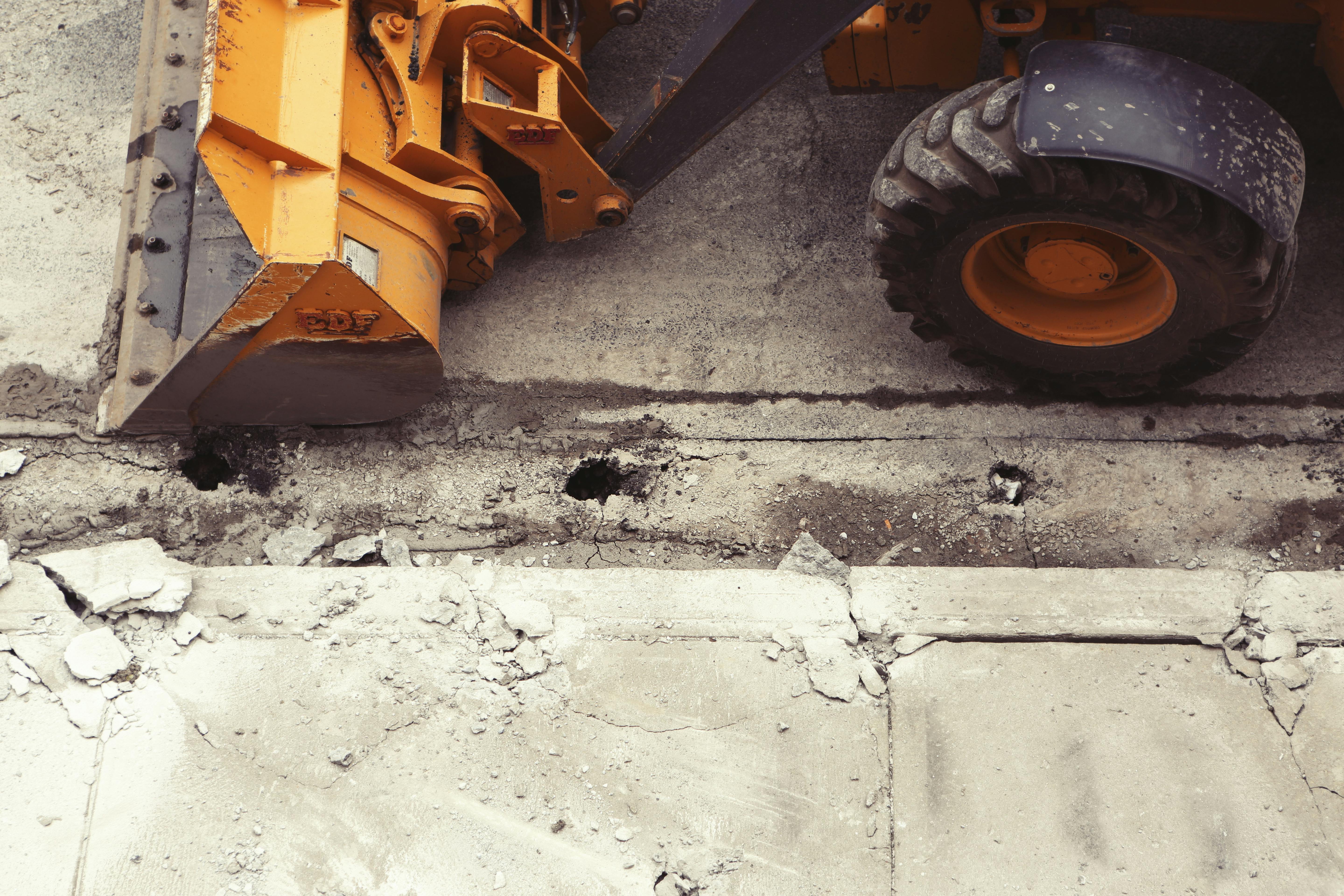
- ERP Software
How to Reduce Failure Costs in Construction Projects
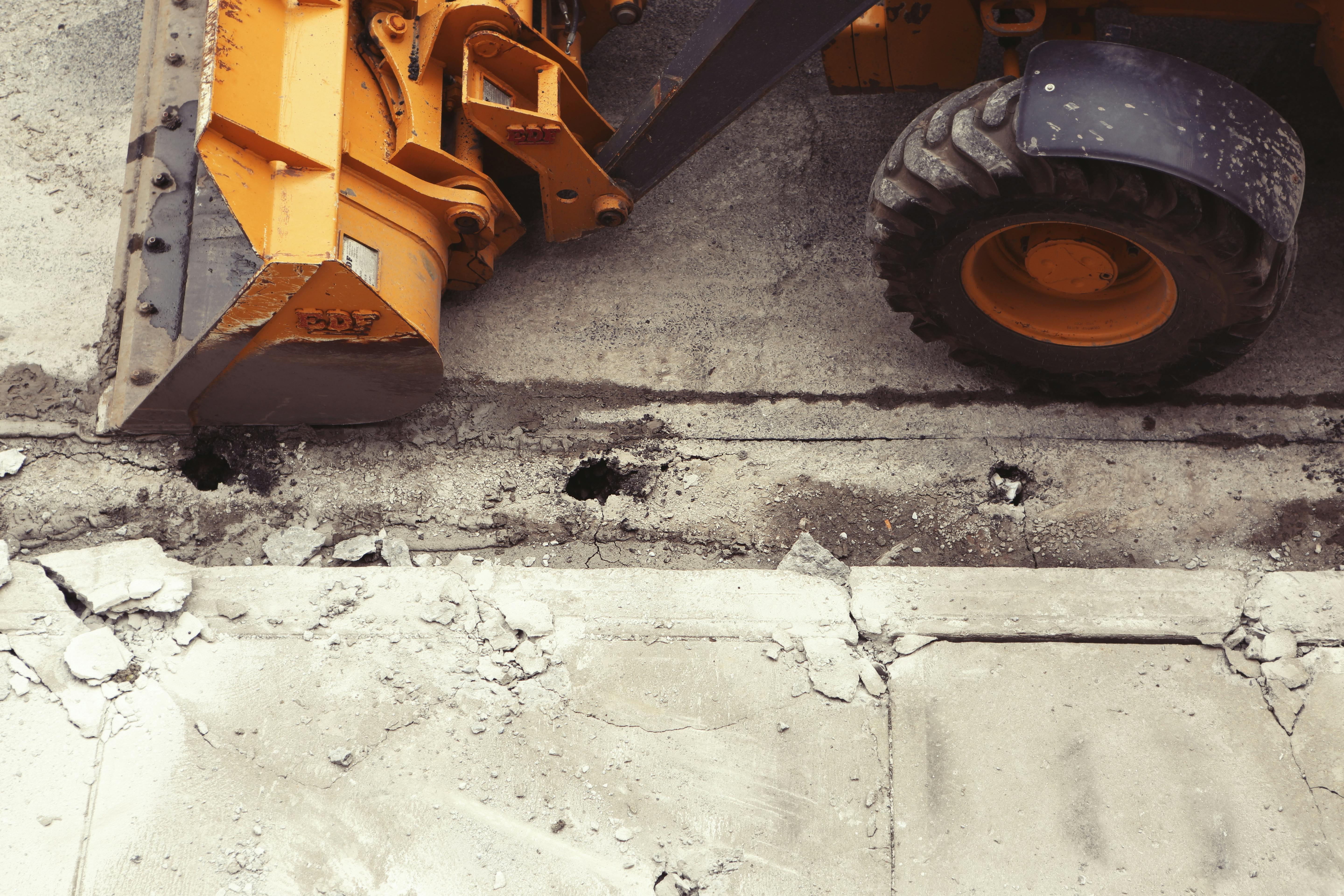
Failure costs contribute to the majority of unexpected expenses in the construction and infrastructure industries. Did you know that these costs run into billions every year in the Dutch construction industry alone? It’s a large and growing problem. Especially when working with multiple contractors on large projects, maintaining control over the financial status of a project is notoriously difficult. So, how can you get a grip on ongoing projects to reduce your failure costs?
Where Do Failure Costs Originate?
Failure costs are additional expenses that arise at various stages of a project. While some extra costs are beyond your control—such as those due to delays caused by bad weather or the limited availability of third parties—most failure costs result from errors. These errors occur in planning, execution, and communication between the different parties involved. The good news is that construction and infrastructure companies have the power to take control. So, how can they achieve this?
Gaining Control with a Modern ERP System
Construction and infrastructure companies can—literally—profit from using a modern and central ERP system. When all project data is processed in one system, project administration becomes easier to monitor. This provides companies with real-time insights into ongoing projects, helping them proactively manage budgets and deadlines, thereby reducing failure costs. How does this work, exactly?
-
On-Site Administration
Most ERP systems include user-friendly mobile apps that allow for project administration on-site. When construction workers log their hours and materials used immediately after their shift, the administration is updated instantly. This provides planners and managers with immediate information, enabling tighter control over budgets and deadlines. -
Improved Work Planning
With better insights, project planners can more accurately predict the labour and materials needed. This allows for more precise team scheduling and improved purchasing and distribution of materials, ensuring everything and everyone is available at the right time and place. This ensures project deadlines are met. -
Enhanced Material Procurement
When purchasers work with up-to-date information, they can ensure materials are procured under the best (pricing) conditions. A well-organised procurement process also guarantees that the right materials arrive at the right time and place, allowing on-site work to begin without delay. This prevents projects from coming to a standstill due to a lack of materials. -
Sharing Information with Third Parties
Over the years, construction and infrastructure projects have increased in size and scope. It’s now common to work on projects involving multiple contractors, suppliers, and other partners. A modern ERP system facilitates the integration of third parties into your project administration. Today, third parties can log their hours, materials, and other costs via smart apps and portals, giving you a comprehensive view of ongoing projects and greater control. -
Learning from Projects
When all processes are captured in a central ERP system, used by all departments at all stages of a project, it provides more than just insights—it enables data analysis. This allows construction and infrastructure companies to learn from past projects, leading to more efficient execution of future projects.
A Significant Change
Real-time insights into the costs and progress of projects? It’s possible! However, success depends on the widespread adoption of the ERP system. The entire organisation must consistently use the system, processing information accurately and promptly. This is a significant change for many companies in this industry, where departments are often given considerable freedom to adopt their own practices. Successful change is closely tied to effective change management. At Emixa, we guide organisations through these changes, ensuring everyone in the organisation makes optimal use of the system.
How to Implement a Modern ERP-system
Emixa supported a renowned construction company with the large-scale implementation of an ERP system, alongside a related data structure and warehouse. This made the status of all large projects available throughout the company and in real-time.Conclusion
Reducing failure costs starts with gaining control over your processes, systems, and organisation. Standardisation helps you maintain control over your operations and the financial status of your projects. Interested in learning how to put this into practice? Get in touch, and we’ll explore how you can take control and reduce your failure costs.
Author: Vincent Nieuwland
Published date: August 26, 2025
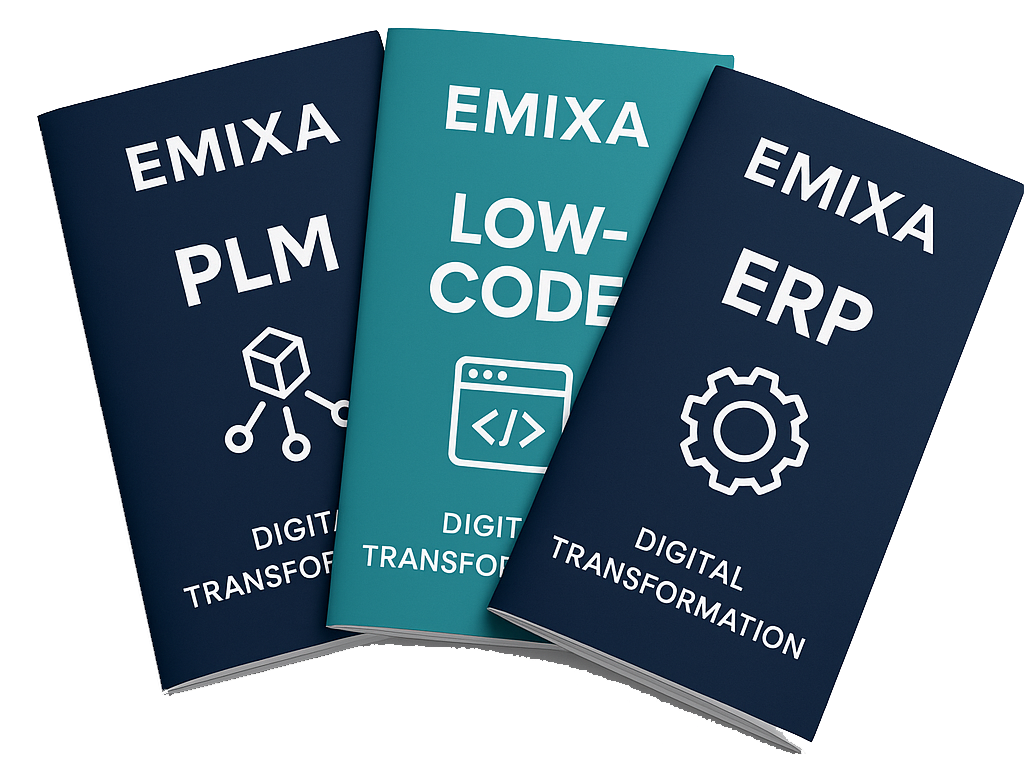
Explore our Technology. Access our downloads center.
Access NowStart your Digital Transformation with Emixa
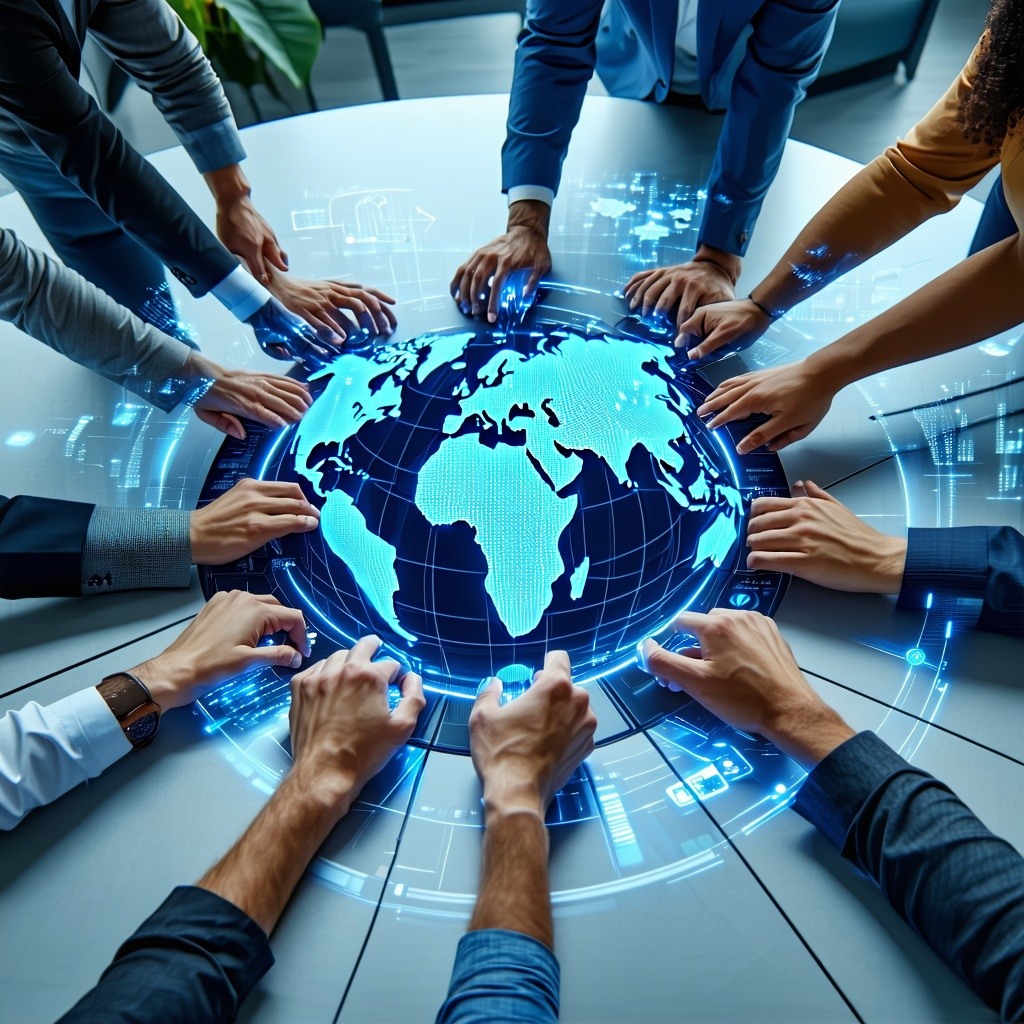
We help businesses transform their digital future with cutting-edge technology and strategic products & services