Transforming from Static Blueprints to a Dynamic Digital Factory
Last edited on Aug, 08 2025 03:25:17 PM
Reading time: 6 minutes
Written by Bart Stuve
Table of contents
Share article
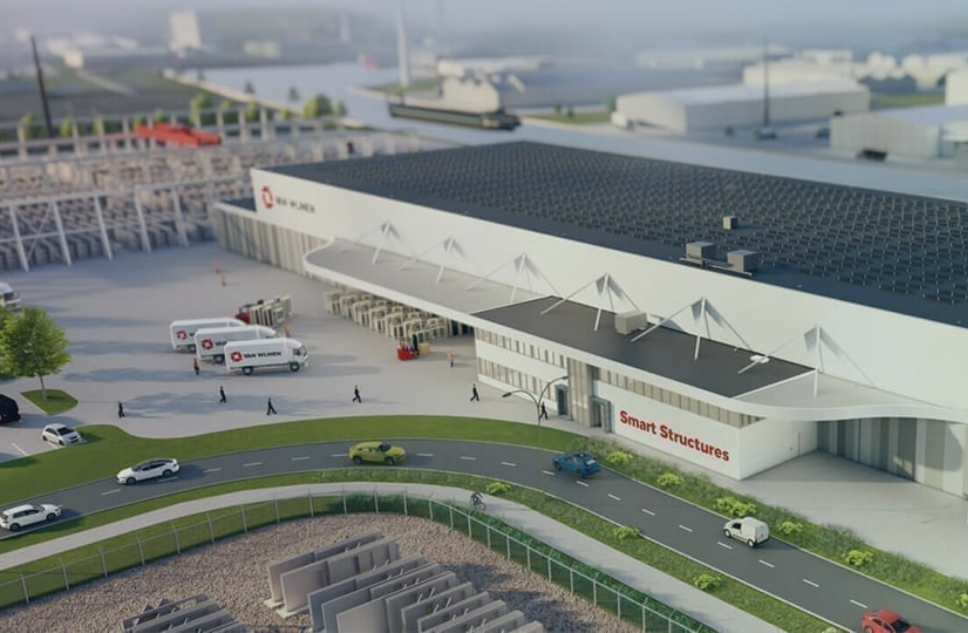
Van Wijnen is a Dutch company in the construction sector, committed to environmentally friendly building for the next generation. Operating from 25 locations across The Netherlands, Van Wijnen is involved in the development, construction, management, and maintenance of buildings and homes.
With the high demand for housing in The Netherlands and a shortage of affordable homes, Van Wijnen recognises the need for a different approach to construction. The scarcity of skilled workers in the industry further intensifies the challenges in housing construction. To address these issues, Van Wijnen is increasingly focusing on industrialised construction, aiming for faster, more cost-effective, cleaner, and circular building methods.
A digital production process
To meet the high demand for housing in the coming years, a substantial number of homes need to be built. Van Wijnen's goal is to realise 4,000 homes per year in the upcoming years. To achieve this, Van Wijnen has invested in a dynamic (or in other words: digital) design, development, and production process.
This digital production process takes shape in a greenfield housing factory. In this future factory, there are large steel tables on which a mould is built using a robot. By using a high degree of robotisation, the problem of skilled worker shortages in construction is also partially solved. The tables with moulds move like a carousel through the factory. At each point where the table stops, value is added, such as reinforcement steel, electrical boxes, window frames and structural lifting and coupling facilities. After adding all the components, concrete is poured, and elements like walls, facades, or floors are prepared. These elements are then put in a controlled environment to cure, all part of an automated process. On-site teams later assemble these components, maintaining a rapid pace, completing one home or two flats each day. This automated process, with its scale and variety, ranging from ground-based homes to flats and gallery flats, all produced in a single housing factory, stands out as unique in the construction industry, not just in the Netherlands but beyond.
The added value of simulation
Simulation serves a crucial role in assessing the viability of an automated process designed to manufacture prefabricated elements for 4,000 homes per year. By transforming the initial static layout drawing into a dynamic scale model, different scenarios can be evaluated. Siemens Tecnomatix Plant Simulation allows Van Wijnen to analyse the manufacturing facility's capability to produce a significant number of components within the desired timeframe. This simulation involves replicating the plant, production floor, machinery, and personnel to examine and validate production changeover times. With various machines assigned different tasks, aligning them seamlessly becomes essential. This software empowers Van Wijnen to optimise machine configurations successfully, ensuring the achievement of the goal to manufacture 4,000 homes each year.
"Through our simulations, we gained early insights into the optimal machinery layout. The dynamic factory simulation helps uncover potential errors, allowing for early identification and resolution of bottlenecks. This not only instils confidence but also offers the flexibility to test optimisations cost-effectively." - André Klouwen, Deputy Director of Technology at Van Wijnen Components
Save costs and maintain oversight
An increasing number of companies establishing a greenfield production facility opt to simulate a dynamic version of the future factory or production hall before its physical construction. The ability to foresee and test the flow of your factory in advance, ensuring that your machinery and desired production can be realised. Knowing the required number of operators to achieve the projected and determined production levels. Despite the complexity of the process, Siemens Tecnomatix Plant Simulation can preserve clarity and save costs.
We are very proud to be part of the future of living! While prefabricated homes have been around for some time, they haven't been produced at this volume. Tecnomatix Plant Simulation is the solution for intricate processes, transitioning from static drawings to a dynamic, digital version of your factory!
Would you like to get started with a simulation of your production environment? Contact us directly.
Last edited on Aug, 08 2025 03:25:17 PM
Reading time: 6 minutes
Written by Bart Stuve
Share article
Also see..
OverviewFAST: Turning Your Data Ambition into a Clear Action Plan
Many companies have ambitious data goals. Whether it involves modernising an outdated data...
Read more ⟶AI as a Tool to Optimise Last-Mile Delivery
Consultancy.nl, the platform for the consulting industry, published an article about the...
Read more ⟶Emixa Celebrates Strong Debut at the 2024 Computable Awards
Last night (Thursday, 27th November), Emixa proudly attended the 2024 Computable Awards, held at...
Read more ⟶