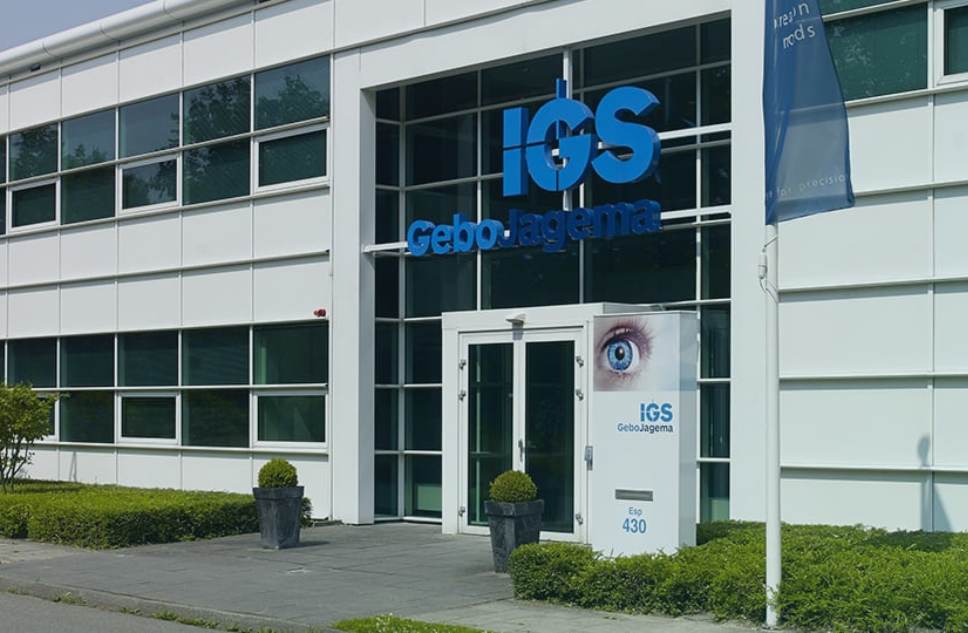
- PLM
Smoothly Optimise your Production Process with Simulation
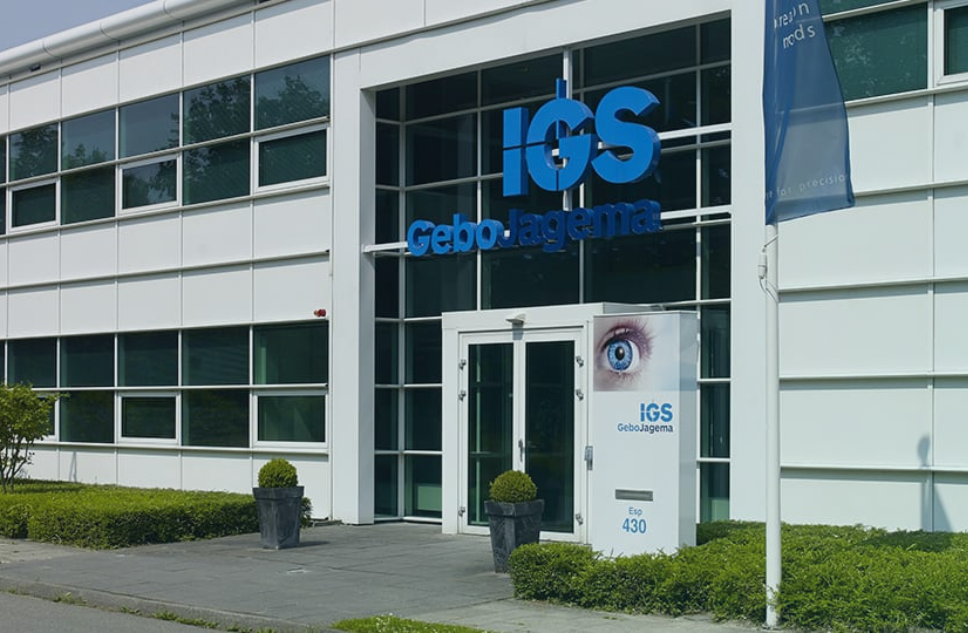
IGS GeboJagema is a full-service partner in the healthcare industry, specialising in high-volume moulds. With a strong belief in delivering the highest quality in all their endeavours, the organisation enables healthcare companies supplying products on behalf of a brand supplier to produce top-notch items in large quantities. The moulds are produced with high precision tolerances, which requires high accuracy in engineering, manufacturing and validation. This allows them to offer an end-to-end solution encompassing design, engineering, qualification and supporting services to all their customers.
“We dare to innovate!” - Rob Doorakkers, Chief Innovation Officer at IGS GeboJagema.
To meet the high precision requirements, being able to tackle problems that may arise during the injection moulding process is an important step. These problems are often a combination of product geometry and the materials to be injection moulded, such as:
- Detecting air traps: Trapped air causes bubbles or voids in the products and can lead to surface finish issues. Using Moldex3D allows for visualisation of potential air traps in advance.
- Detecting heat concentrations: Heat concentrations in the product and in the mould indicate where cooling can be optimally applied and provide insight into the required cooling time.
- Detecting flow patterns: Wavy lines visible in the final product indicate how plastic fills the mould cavities and highlight potential issues.
- Detecting the pressure expected in the mould
In the past, simulations were outsourced due to a lack of in-house expertise and manpower. To speed up the simulation of the injection moulding process and add value for clients, IGS GeboJagema chose to bring simulation in-house. IGS GeboJagema selected Moldex3D based on its seamless integration into existing processes, combined with associated costs, capabilities, and support for software implementation.
"The assistance we received during the procurement, initiation, training, and the promptness in addressing technical queries throughout simulations significantly influenced our decision to opt for Emixa Industry Solutions." - Rob Doorakkers, Chief Innovation Officer at IGS GeboJagema.
The implementation of Moldex3D has revolutionised IGS GeboJagema's simulation process, resulting in a faster, more optimised, and thoroughly validated production process. Fast adjustments during mould validation have become a reality, and simulation serves as a crucial tool for validating optimisation ideas before committing to costly mould implementations. This software allows the proactive detection of issues like air traps, heat concentrations, and flow patterns, preventing expensive mould modifications and streamlining the validation process. Moving forward, IGS GeboJagema plans to engage in multiple straightforward simulations as part of the quotation preparation process, gradually building the necessary expertise to conduct extensive simulations independently. The company envisions a future where they continually explore and expand the possibilities within simulation.
"What sets us apart is our ability to strategically place elements such as venting and cooling in advance, significantly reducing the optimisation timeline. Conducting cooling simulations provides a comprehensive view of temperature dynamics in the mould, enabling us to effectively inform and persuade customers during the design phase." – Rob Doorakkers, Chief Innovation Officer at IGS GeboJagema
Discover the power of Moldex3D for performing injection moulding analysis.
Author: Bart Stuve
Published date: August 26, 2025
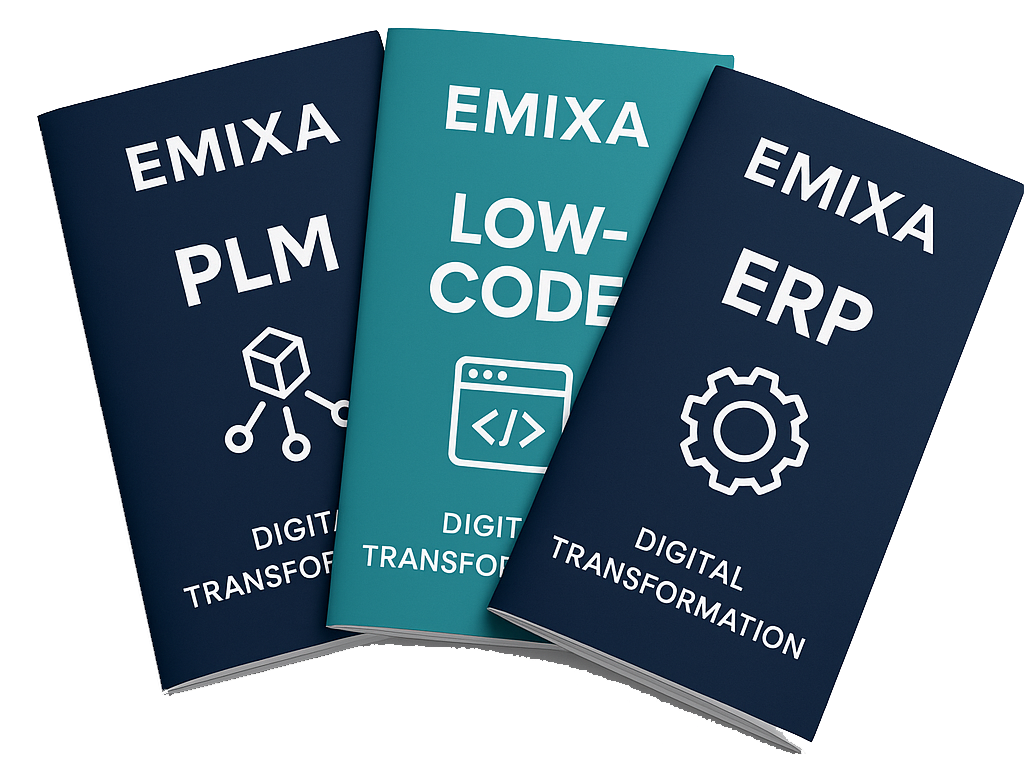
Explore our Technology. Access our downloads center.
Access NowStart your Digital Transformation with Emixa
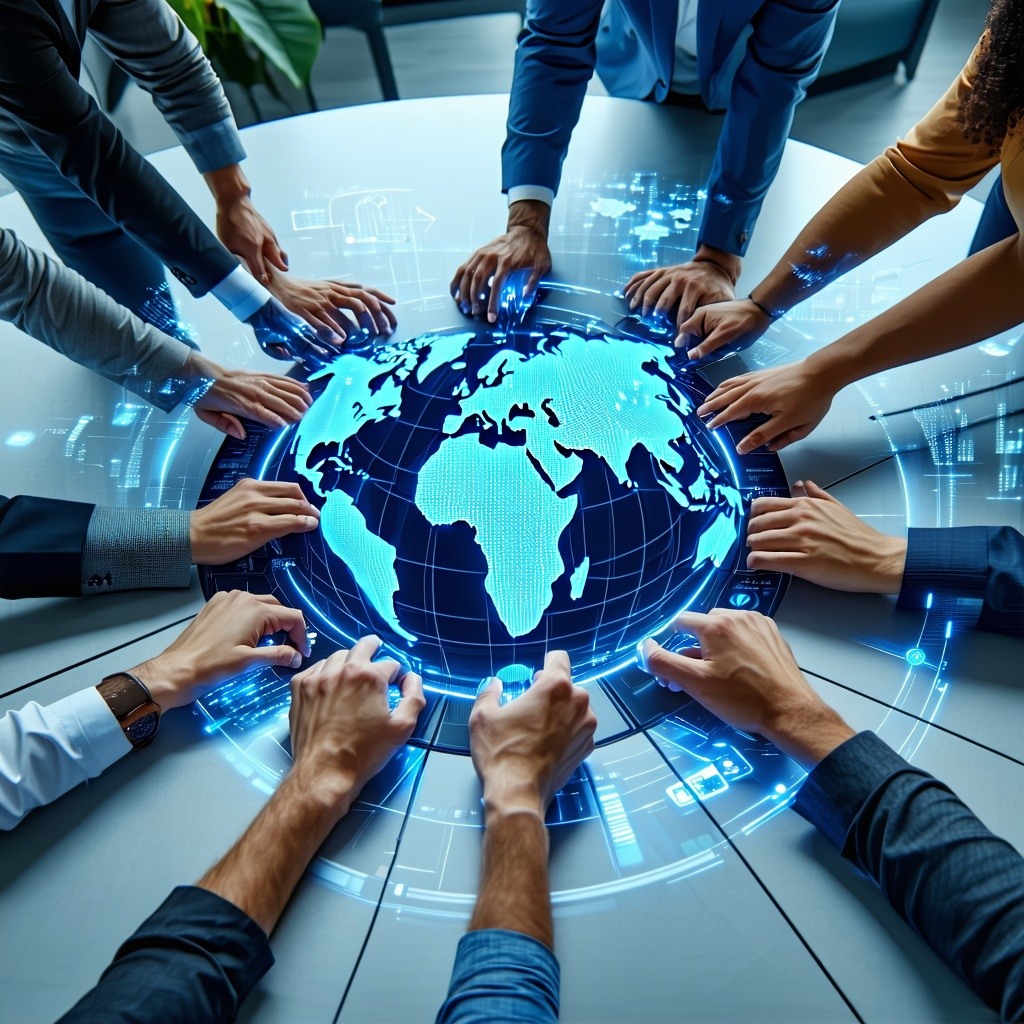
We help businesses transform their digital future with cutting-edge technology and strategic products & services