The Benefits of Virtual Commissioning of Machines
Last edited on Aug, 08 2025 03:20:44 PM
Reading time: 6 minutes
Written by Bart Stuve
Table of contents
Share article
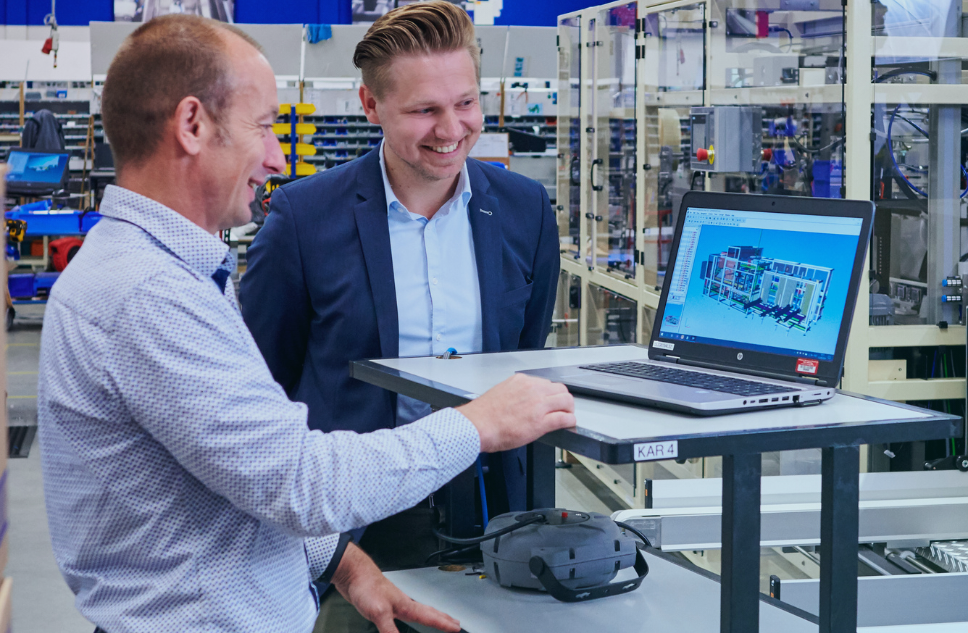
As market demands for new products intensify, production companies face the challenge of adapting existing lines and commissioning new machines faster. Digital models offer a solution by allowing testing and validation even before the physical systems are installed.
The key focus here is time savings, a critical factor in the highly competitive manufacturing landscape. The market's increasing demand for new products and variations shortens product life cycles, emphasising the need for reduced time-to-market. This time pressure extends to machine or line builders and high-tech suppliers, requiring fast delivery of new machines and adapted production lines.
To meet these demands, companies are implementing complex systems and automation, leading to a growing presence of electronic components and control code. Before adding a new automation system to your manufacturing process, it's crucial to thoroughly check and test it. This ensures that the mechanical and electronic components in the control system work together seamlessly.
Errors show up too late
Discovering errors too late is a common challenge in the traditional commissioning process. The preparation for commissioning, involving checks and tests, is typically a physical procedure conducted on the actual machines. Consequently, commissioning occurs at the end of the development cycle, post-engineering and production completion. When errors surface at this stage, rectifying them often demands a substantial amount of time and financial resources. Identifying these problems earlier in the process could have led to quicker and more cost-effective solutions. And that's not to mention the extra pressure imposed by the client when the project is delayed. The client then cannot start production as planned and inevitably loses a lot of money.
Another scenario involves adapting an existing production line, which requires a halt to make necessary component adjustments and conduct a test run. This interruption has considerable effects, causing production delays and significant time losses during testing.
In practice, we see that many companies still follow this conventional approach, conducting machine or line commissioning on-site. This leads to considerable time loss compared to competitors who conduct digital commissioning tests. With a digital model, a digital twin of the production line or machine, companies can virtually simulate line adjustments or the integration of a new machine.
Virtual commissioning
In virtual commissioning, the written PLC code is linked to the virtual model instead of the physical one. This allows the validation of the entire line or machine operation at an early stage, with engineers visually observing the machine's performance. This visual aspect proves crucial in identifying minor errors or problems that might otherwise go unnoticed.
If issues arise in the simulation, it is possible to quickly adjust the necessary elements within the digital model. This approach enables checking and adjusting the complete process control virtually before proceeding to the actual on-site construction once everything is in order.
Digital models provide advantages for clients as well. They gain insight into the machine's eventual operation at an early stage, ensuring clear communication and refining client requirements early in the process. It also allows clients to train employees worldwide to operate the machine before the physical machine is built.
Utilising the digital twin for designing, validating, and commissioning a line or machine has numerous benefits, including:
- Reduction in the total development time of each project
- Shorter commissioning period
- Reduction in total costs
Importantly, this method not only results in significant time and money savings but also allows the existing line to continue production during the adaptation phase. It also ensures better scheduling and execution of the actual, physical adaptation of the line, minimising the impact on production staff.
Get in touch
Shifting to virtual testing and setup is a big move. At Emixa, we take a practical step-by-step approach. Curious to learn more? Contact us, and we'll provide further details.
Last edited on Aug, 08 2025 03:20:44 PM
Reading time: 6 minutes
Written by Bart Stuve
Share article
Also see..
OverviewFrom Warehouse to Doorstep: A Conversation on Last Mile Optimisation
The final delivery step to the customer, the ‘Last Mile,’ may seem simple. However, it is often one...
Read more ⟶AI as a Tool to Optimise Last-Mile Delivery
Consultancy.nl, the platform for the consulting industry, published an article about the...
Read more ⟶Agile Way of Working? Beware of These 6 Pitfalls
Agile working: empty buzzword or indispensable strategy? Some see Agile as the holy grail for...
Read more ⟶