Future-oriented construction thanks to modernization of the IT landscape
Last edited on Aug, 12 2025 09:12:59 AM
Reading time: 3 minutes
Written by Jan Wijbren Dijkstra
Table of contents
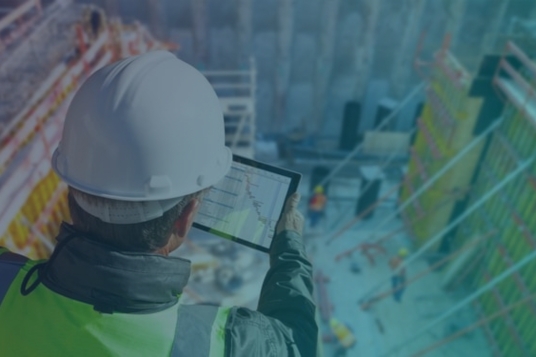
Margins within construction are wafer-thin. High costs, relatively sensitive schedules and the switch to maintenance contracts are the basis for this. As a unique additional challenge, construction companies run the risk of one miss erasing all profits for the year. To build for the future, measures are needed that mitigate these risks. A modernization of the IT landscape offers a solution.
A perfect, future-oriented IT landscape in construction offers:
- central storage of expertise and knowledge;
- overview of all construction activities;
- support for internal collaboration;
- links for external collaboration and transfers;
- control over the supply chain;
- automation or robotization of steps in the chain.
Central storage of expertise and knowledge
The aging of the population is strongly noticeable within the construction industry. A new generation of employees needs to be trained, but the enthusiasm among school leavers is low. A high turnover of experienced employees who are ready for retirement hinders the transfer of knowledge and expertise. This makes it difficult to find, train and retain professionals. Complex projects are being delayed and accidents and incidents are increasing across the board of construction activities.
Digital support for expertise and knowledge transfer is therefore essential. The knife cuts both ways. On the one hand, knowledge and experience is no longer only in the minds of employees because it is stored centrally, on the other hand, digitally stored knowledge can be translated into innovation. A central source of information fuels further innovation. It serves as inspiration to develop best practices.
The better the digital knowledge assurance, the greater the use of this knowledge in practice. Thanks to this flywheel principle, success leads to more success.
By working with photos and videos, knowledge is easy to provide and record. A side effect of the visualization of knowledge is that it can also be used as a 'see-through sheet'. People can use the images to check and improve their own work.
Overview of all construction activities
Risk management is essential to survive as a construction company. One project gone wrong can wipe out a year's worth of profits. To make the pain worse, it often turns out that problems arose early on. Earlier intervention, for example by distributing resources differently across projects, could have prevented worse.
The cause of this problem lies in the silo approach. Each project is approached on an individual basis. Connecting construction projects provides an overview of budgets, available resources, schedules and subcontractors. This data is not only related to one project, but is included across the entire scope of the work in progress. This makes it possible to gain mutual insight into priorities and make adjustments with available resources.
Integrated data storage also provides benefits after delivery. It provides the basis for monitoring maintenance contracts and provides good substantiation for new quotations. Results from comparable projects help you to quote razor sharply while maintaining a good margin. Internally there is continuous insight into project progress and project results. This information helps to optimize planning and management of subcontractors.
Support for internal collaboration
Without insight into the scope, schedule and costs, no project will get off the ground. Structured document management has rightly retired carbon paper and clipboards. But that is the beginning of innovation, not the end point. By further digitalizing internal collaboration, quality, safety and profitability can be improved.
By supporting internal collaboration in a structured manner, planning becomes easier and costs are always transparent. This makes it easier to coordinate the activities of employees, suppliers and subcontractors. Everyone involved in a project has easy access to the latest 2D and 3D models. All other documentation surrounding a project is available to everyone.
Anyone who takes into account 25 years of operation, facilitation, maintenance and sustainable demolition when realizing the asset will benefit from this throughout its entire lifespan. This collection of data forms a so-called Digital Twin. This allows maintenance staff to view status and track repair and warranty information. The builder accurately records the lifespan of deployed resources and takes this into account in new projects. In the context of circular construction, it is clear at the end of the lifespan which materials can be reused. This approach requires active involvement of all responsible parties.
Links for external collaboration and transfers
The complexity of construction projects is increasing. Higher requirements and more advanced materials are partly responsible for this. But the desire to have maintenance carried out by the contractor after delivery also plays a role in this. To continue to operate profitably, it is important to collaborate with specialized partners and subcontractors on every project.
Those who find partners quickly can respond to quote requests earlier and better. This requires knowledge of your own organization, good connections with third parties and a way to quickly share concepts with each other. Construction Information Model software (BIM) offers a solution here. You can coordinate this collection of construction data using the software. By linking BIM to ERP and project management, agreements can also be properly recorded and used in the tendering part of the process.
The collaboration becomes closer as digitalization is better organised. By fully supporting internal processes digitally, it becomes easier to also allow external parties to collaborate. Partners who also work digitally are desirable. This allows connections to be made that further simplify collaboration and transfer.
Control over the supply chain
Delays entail costs. Better control over the supply chain reduces these costs and offers planners more certainty. The chain for builders consists not only of suppliers of building materials, but also of subcontractors and rental companies of large equipment such as cranes. By digitally integrating this chain with your own resources, control over projects is increased.
For construction companies, smarter planning is a first step towards better margins. The digital resources that make smart planning possible can also be used to gain more control over the chain. Statistics on delivery times and reliability of suppliers can play a role in planning new projects.
If those suppliers also work with advanced digital support, then a link is obvious. Technology such as IoT (Internet of Things), which makes it possible to see the exact location of equipment at any time, makes it possible to work with more precise delivery times. The use of BIM makes it possible to plan prefabricated materials in such a way that they can be installed immediately upon delivery.
Automation, robotization and 3D printers
Traditionally, construction has the principle of intermediate checks. For example, goods are received at the gate of the construction site, but only paid for when the project manager approves the invoice. With the right automation, the person responsible on site can check the goods upon receipt at the gate, after which all further steps are handled automatically. This saves a lot of time because other parties involved only have to deal with deviations.
More time savings can be achieved with time registration. It still happens too often that the project manager has to approve the hours of external employees twice: once for inspection and once for the software. By smartly registering controlled hours, it is possible to link them directly to the corresponding invoices. With one precise control at the front, work can be done much more efficiently at the back.
Robots, cobots and 3D printers offer unprecedented opportunities. Robots can perform repetitive tasks very quickly without human input. Robots strengthen employees by directly assisting them and simplifying tasks. The added value of cobots increases if they can draw from the central store of expertise and knowledge. The potential of 3D printers is unprecedented. A good example: when pouring concrete for a villa and apartment complex in China, the use of 3D printer technology saved 30 to 60 percent of building materials and the execution was 50 to 80 percent faster.
Future-oriented building
Future-proof construction companies have control over costs and work with tight schedules. Modernizing the IT landscape makes it easier to meet these two essential requirements. In addition, it offers room to quote more competitively, collaborate more smoothly and deploy people more effectively. Organizations that innovate are given the space to transform. This helps them respond more effectively to the market of the future and operate more profitably.
Get in touch
Ready to make a business change? At Emixa, we'd be glad to share our comprehensive insights. Contact us to discover how our approach can help your organization thrive in the cloud era. Let's embark a journey towards enhanced efficiency and effectiveness together!
Jan Wijbren Dijkstra
Jan Wijbren Dijkstra is Senior Lead Consultant ePPM at Emixa Managed Services. With more than 25 years of experience with SAP and ePPM, he knows how to translate specific processes into solution in or related to SAP, with efficiency and continous improvement. His business knowlegde is in the domain of managing projects within several branches and organisations, primarily in Engineering and Construction.
Last edited on Aug, 12 2025 09:12:59 AM
Reading time: 3 minutes
Written by Jan Wijbren Dijkstra
Also see..
OverviewReview of Expert Event 'Industrialization of Construction'
March 24, 2022 - Experts from the construction and manufacturing industry come together to inspire...
Read more ⟶What SAP S/4HANA deployment options are there available?
SAP continues to emphasize ERP in the cloud. With monthly new releases, S/4HANA Cloud has become...
Read more ⟶Process Mining: The Accelerator for a Successful S/4HANA Migration
You may already be familiar with SAP's future plans: within the next five years, support from SAP...
Read more ⟶