Business Challenges
- Mould outsourcing
- Altering approved designs
- Mould modification expertise required
Keys to Success
- Niche focus on mould modification and testing
- Expansive facilities for in-house testing
- Integrated CAD/CAM system for swift adaptations
Results
- Faster time-to-market
- High first-time-right rates
- Diverse one-stop solutions
Case study Surtechno
Mould service company Surtechno plays a pivotal role for European car manufacturers. With 35 employees, the Surtechno modifies, repairs, and refines moulds for producing large plastic components, serving clients like Audi, BMW, Mercedes, Opel, and Porsche. These clients demand top quality with rapid turnaround times, and Surtechno possesses the expertise and equipment to meet these demands.
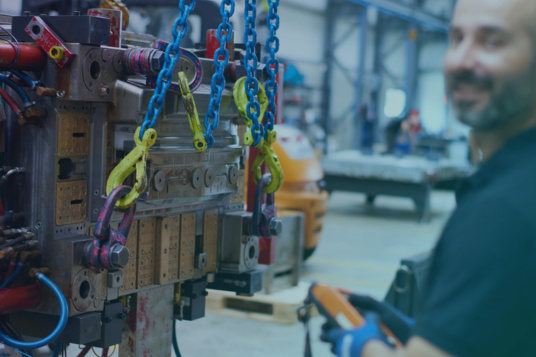
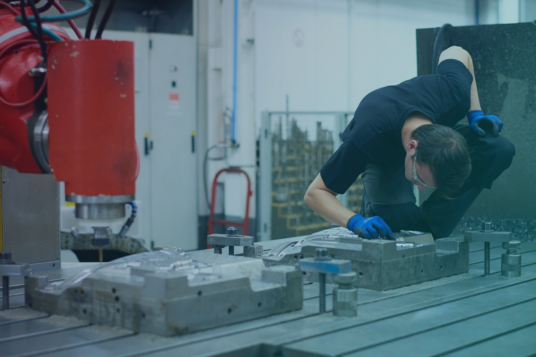
Business Challenges
In 2005, Surtechno ceased the production of moulds as the manufacturing of larger components such as bumpers, door panels, and dashboards moved to Asia, benefiting from lower production costs. This transition, however, brought new challenges. With increasing complexity in mould designs and heightened client expectations, the need for post-design alterations has become more frequent. This poses a significant issue when moulds, already en route to Europe, require modifications. Returning them to Asia is impractical due to the time and additional costs involved. As a result, suppliers are now compelled to either invest in their own modification facilities or partner with a proficient company like Surtechno, which specialises in modifying, repairing, and enhancing moulds to meet these evolving needs.
Keys to success
To adapt to market shifts, Surtechno pivoted to specialise in a niche sector: refining and modifying moulds and conducting pre-production tests for major suppliers. This strategic shift necessitated substantial investments in expanding their facilities, machinery, and testing capabilities. Consequently, Surtechno added a 2000 square metre building, enabling them to perform in-house adjustments and testing of moulds before dispatching them to production sites. Surtechno also upgraded its software capabilities to stay ahead, integrating Siemens NX™ CAM with its existing NX™ CAD environment. This integration allows designers to modify 3D digital models according to client needs while CAM experts begin programming and simulation concurrently. The CAD/CAM software enables Surtechno to evaluate and simulate the milling process, ensuring readiness for immediate action upon a mould's arrival from Asia. This setup establishes direct feedback loops for quick incorporation, testing, and refinement of design changes. Surtechno's commitment to adaptability also involved upskilling several employees, from machine operators to CAM programmers. These strategic changes have effectively positioned Surtechno to meet the rapid demands of today's mould market.
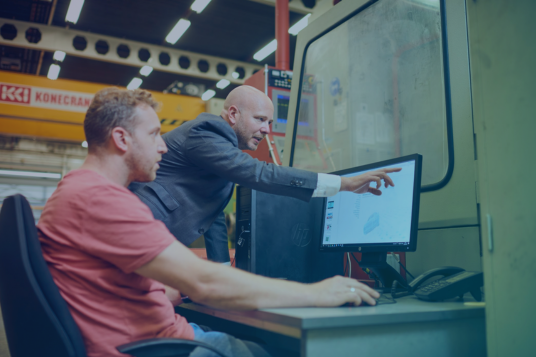
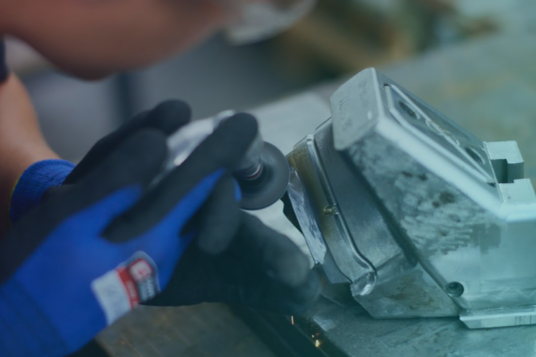
Results
The project delivered numerous positive outcomes. Firstly, it reduced the time-to-market, allowing products to reach the market faster. Additionally, there was a significantly higher first-time-right rate, achieving accurate results and product quality on the first attempt. Providing a one-stop shop with a comprehensive range of solutions was also integral to achieving success. Moreover, the client portfolio includes almost all major European suppliers, showcasing the company's growing trust and reputation in the sector.
Related Cases
%2015%25-3.png)
Revolutionizing Design with Siemens NX™ Integration
Pilipili, an industrial design agency, used Siemens NX™ to overcome software limitations, enabling them to create intricate designs, streamline parametric aspects, and achieve remarkable efficiency, resulting in shorter project timelines and enhanced ability to tackle complex design challenges effortlessly.
%2015%25-4.png)
Revolutionizing Precision Machining with NX™ Software
YouniQ Machining, a pioneering startup leveraging Siemens NX™, has revolutionized precision machining by minimizing human intervention, slashing lead times to two days, and achieving an 80% automation rate, transforming the industry's norms.