Business Challenges
- Relying on robotic cells for production goals
- Complex product mix challenges standard tools
- Tools struggle with evolving demands
Keys to Success
- Adaptable tools for a more efficient system
- Cell design planning to prevent resource waste
- Simulation optimisatin for digital twin
Results
- Simulation optimises resource allocation
- Enhanced communication with management
- Improved workflow efficiency
How Oerlikon Eldim Optimised Robotic Workflows with Digital Twins
Oerlikon Eldim (NL) B.V. manufactures and processes components for aircraft engines, meeting stringent quality standards. With over 270 employees, they employ modern technologies such as wire and zinc sparking, 5-axis grinding, laser cutting and drilling, as well as CNC turning and milling.
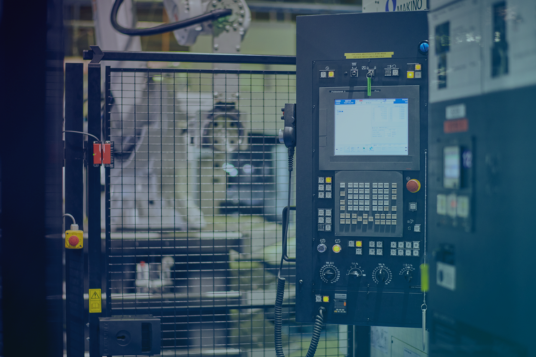
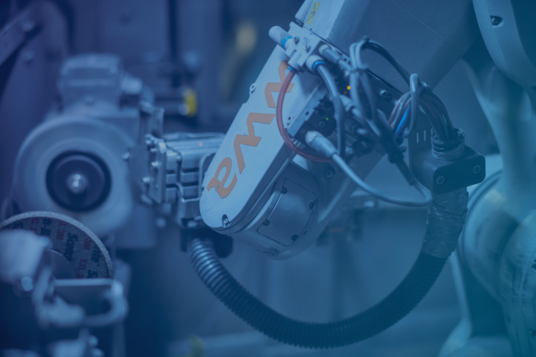
Business Challenges
High-tech production companies like Oerlikon Eldim (NL) B.V. often rely on advanced automated robotic cells to achieve their production goals. However, as product mix complexity increases and time-to-market shortens, these companies frequently use conventional tools to forecast their future performance, posing a challenge for Oerlikon Eldim (NL) B.V.
Keys to Success
Conventional tools like Excel spreadsheets come with significant drawbacks: they're built on assumptions and lack the ability to accommodate dynamic conditions such as machine downtime and operator availability, especially without extensive programming language expertise.
This limitation becomes apparent in detailed throughput information management, which now demands new systems. Assumptions in the design phase of a robotic cell can lead to significant impacts. To ensure the desired output, systems are often designed with safety margins to guarantee production capacity.
However, this approach can result in over-dimensioning, leading to unnecessary costs in additional operators, tooling, and other production assets. Oerlikon Eldim (NL) B.V. recognised an opportunity to reduce initial production resources significantly compared to previous estimates.
By initiating a project to implement Discrete Event Simulation for management decision-making in new robotic cells, the company can now develop a digital twin of an automated robotic workstation.
This simulation model captures dynamic factors often oversimplified or ignored, including expected operator occupancy, workload distribution, and maintenance intervals. Using this model, Oerlikon Eldim (NL) B.V. can optimise resource utilisation in the digital twin and effectively communicate the impact of these optimisations to management, leading to more informed and efficient production strategies.
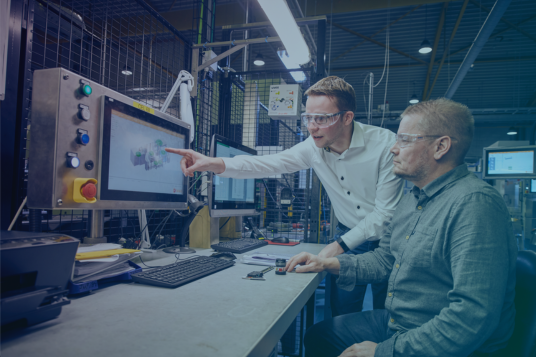
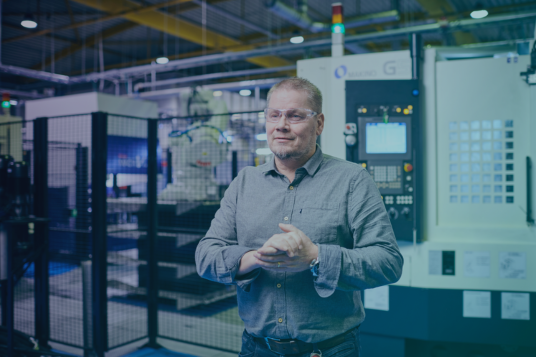
Results
By leveraging Discrete Event Simulation, Oerlikon Eldim (NL) B.V. achieves a comprehensive understanding of dynamic production factors, enabling them to optimize resource allocation throughout the production process. This improved allocation fosters enhanced communication with management, ensuring a more efficient workflow.