Business Challenges
- Respond to aggressive competition
- Accelerate new product development
- Utilize limited engineering resources efficiently
Keys to Success
- Follow a clear technology roadmap
- Use Teamcenter to manage and control all engineering data
- Share data quickly and easily within the company and with suppliers and customers
Results
- Design time for assemblies cut in half
- Drawing and revision updates available across the company within 15 minutes
- Material and weight costs cut through simulation and optimization
Precision Perfected: Elevating Industrial Standards with NX Technology
Norbar was the first company in Britain to commercially manufacture a torque wrench, and early demand was driven by the need to accurately tighten the gasketless cylinder head of the Rolls-Royce Merlin engine used in the Spitfire.Today, Norbar designs, manufactures, calibrates and recalibrates a wide range of products: torque wrenches, screwdrivers, multipliers and calibration equipment. With customers and distributors all over the world and the premiere laboratory for torque in the United Kingdom (UK), it is accredited to test, inspect, calibrate and certify to national and international standards.
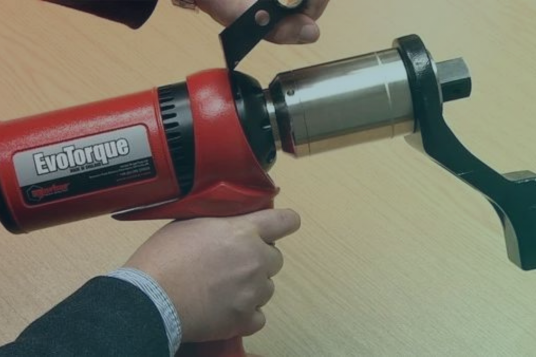
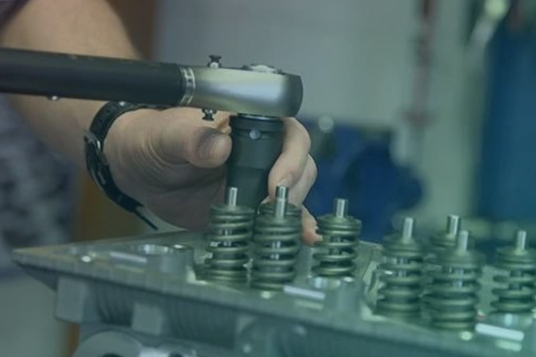
Business Challenges
Using the simple toolset provided by Siemens Digital Industries Software, Norbar moved all its design data, engineering history and documentation from I-deas™ software and Teamcenter® software for the enterprise to NX™ software and Teamcenter on the unified architecture. Throughout this project Norbar was supported by Emixa, a long-established Siemens Digital Industries Software partner. Radini notes, “Having worked with us for 12 years, the specialists at Emixa really understand our business and have done a marvelous job of customization, migration, training and support.”
With authoring and viewing licenses distributed across all departments, Teamcenter is now the company’s engineering backbone. It manages NX, which is used for design, simulation and analysis, and controls all engineering changes. One advantage for Richard Wotherspoon, design engineer at Norbar, is that the company’s information technology (IT) department is now in charge of the Teamcenter database. “This means that I can concentrate on engineering, which is what I am employed to do.” Across the business, Norbar is already seeing improvements in design efficiency, product optimization, workflow, process quality and customer service.
Keys to Success
For Norbar’s engineers, one key benefit of NX is synchronous technology, which allows a designer to work on a part with no reference as to how it was originally modeled. This is particularly valuable when working with legacy data that has no available history. In addition, it confers design freedom because there is no constraint on engineers to work in a particular way.
“NX enables us to work efficiently within an assembly, creating new parts from sketches. We have made a step change in speed; NX is halving design time spent on assemblies. We are also much more confident of what we have created. We can do all the tolerance and interaction checks and know that when we put the product out to the shop floor it’s going to be right the first time.”
NX provides the capability to model structural strength in minutes and simulation is becoming increasingly important at Norbar, not only because it helps to speed up the design process. It also enables engineers to incorporate a degree of optimization. This is particularly relevant for customized engineer-to-order (ETO) products. With very short timescales (typically a week for engineering and four weeks for manufacturing), there is not enough time to carry out physical tests. In addition, making a test unit followed by a production unit would double the cost of any one-off ETO.
The freedom to change parameters, edit the results and view multiple results means that engineers can easily make comparisons. “The overall benefit of simulation is peace of mind, and we are getting results on the screen that we would expect to see in real life,” says Ian Tomlinson, design engineer at Norbar. “Because we are confident about how our parts will work in practice, we can focus on the design. We have, for example, been able to reduce the thickness of a steel reaction plate by 50 percent without affecting its performance. This has cut material cost, and weight too. For Norbar, weight reduction is key to making tools that are less complex, safer and more operator-friendly.”
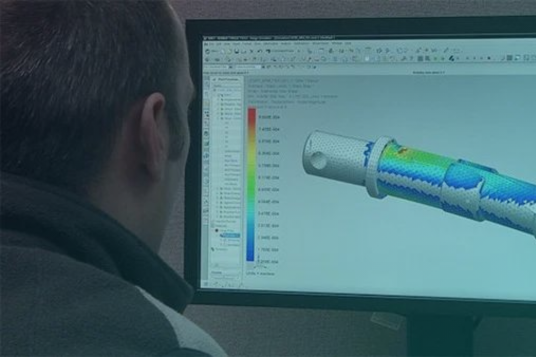
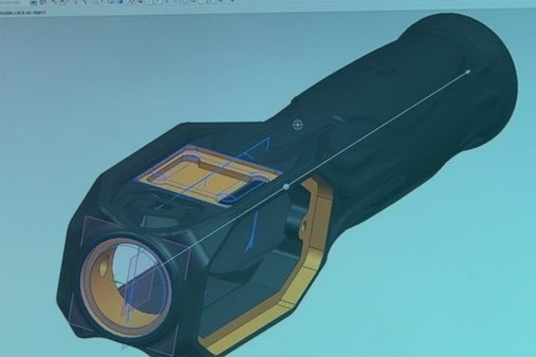
Results
Norbar’s engineering software is fully integrated with Teamcenter; Norbar uses it to store the history of all products it designed over the past decade. That means it is very easy to trace all changes and address any issues. With Teamcenter, Norbar has a system in place that complies with all relevant industry standards covering the secure management of data and processes, including the stringent requirements of the aerospace and defense industry.
“There is no doubt that by adopting PLM we have improved our time-to-market,” concludes Radini. “In the last year, we have released two major new products, the EvoTorque® and the NorTronic®. In addition, we have been continuously extending and enhancing our range of torque wrenches, multipliers and electronic products to meet the demands of our customers. We could not have done that without NX and Teamcenter. That is why we made an investment in PLM; it is all about remaining a premier brand at the forefront of innovation.”