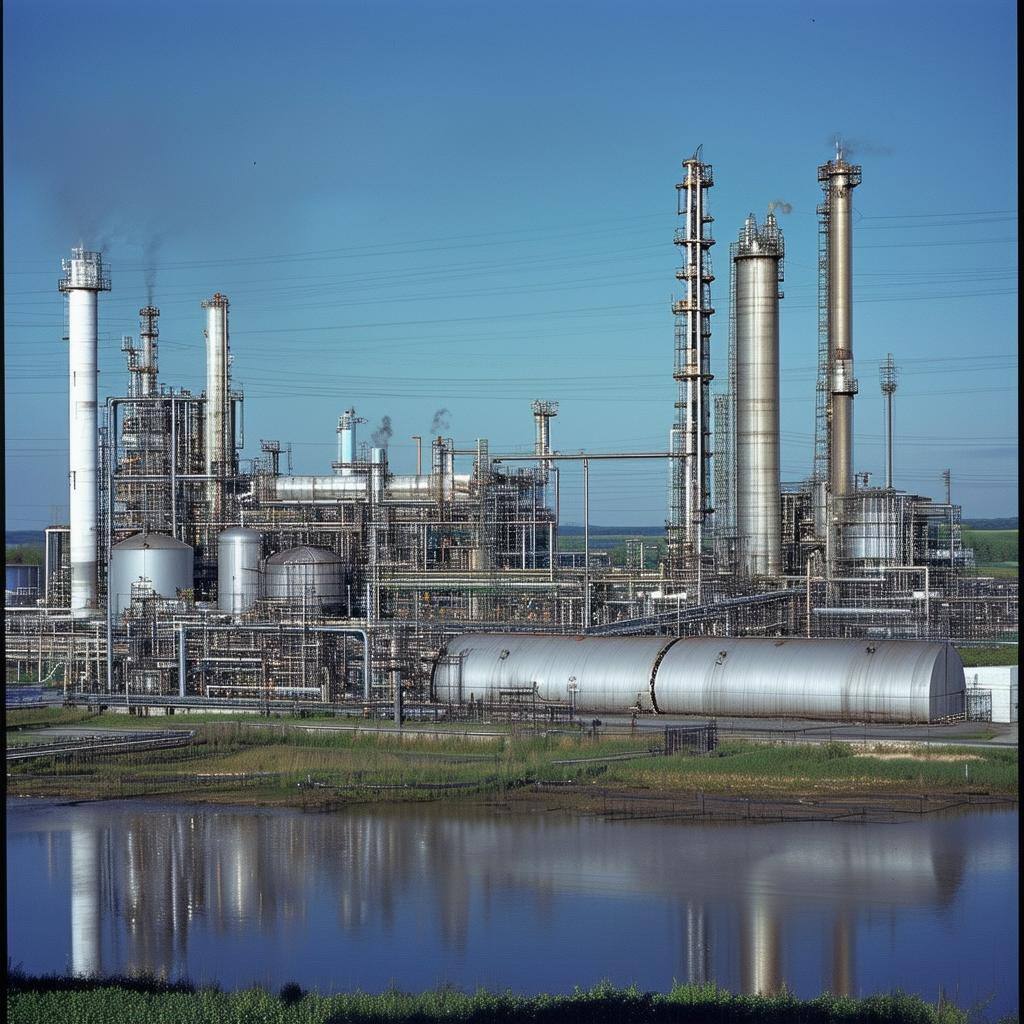
Chemical company Dow is taking an important step towards planned maintenance
Your expert partner in future-proofing your business to optimize and improve
Business Challenges
• Optimize the operational efficiency of Field Planners at Dow Chemicals by leveraging SAP Enterprise Asset Management (EAM)
• Gain a comprehensive understanding of their responsibilities and their actions’ impact on the maintenance process as Field Planners
• Establish a unified method to ensure consistency in data recording and in the coordination of maintenance execution
Keys to Success
• Close collaboration as a unified team between Emixa consultants and Dow colleagues
• Tailor-made training material to teach employees to optimally use SAP within Dow’s specific maintenance process
• A comprehensive coverage of the entire process, ensuring an understanding of the various roles within the maintenance process
Results
• A tailor-made seven-day training course, including a final exam
• Eighteen training cycles, training over 150 field planners, have been conducted to date by Emixa consultants
• A unified method that is followed by the field planners
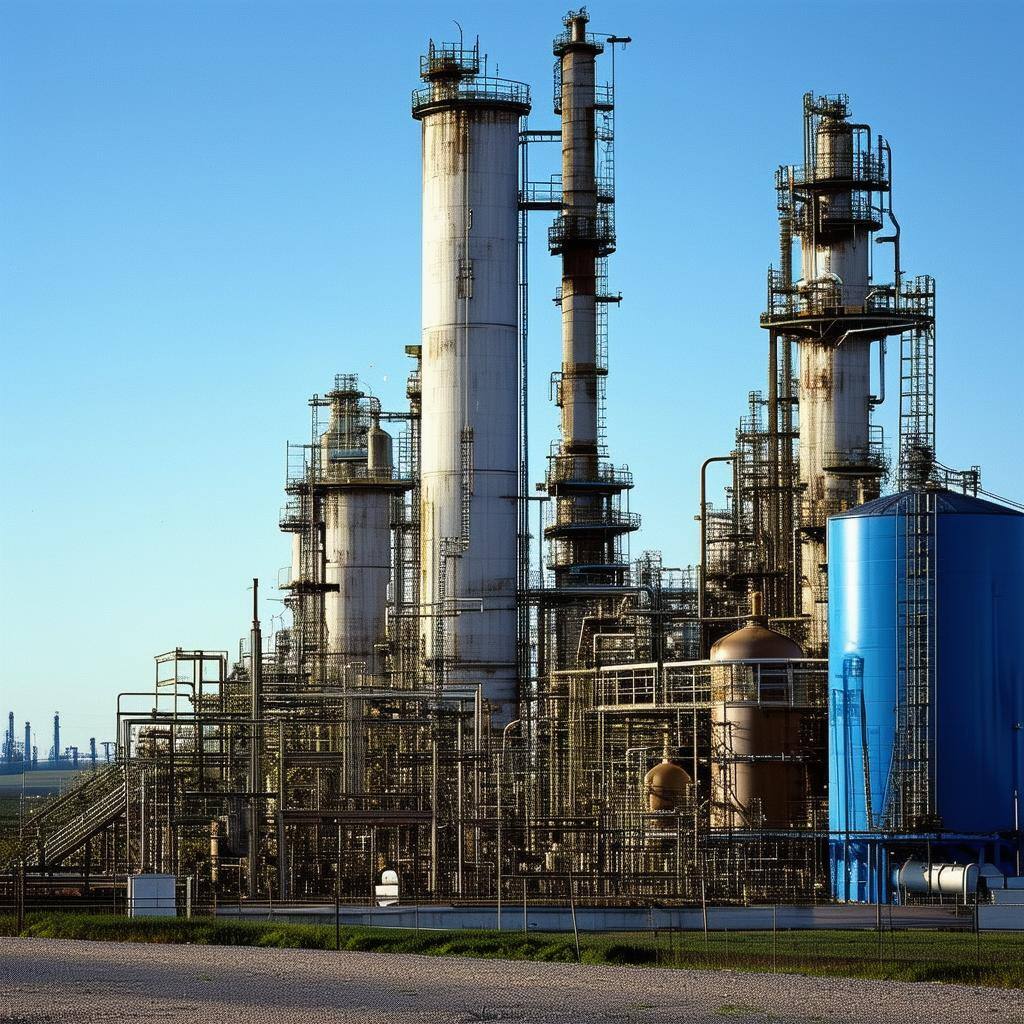
Chemical company Dow is taking an important step towards planned maintenance
The Dow Chemical Company, a global leader in the chemical industry, operates one of its largest complexes outside the U.S. in Terneuzen, Netherlands. This site features three massive crackers that process LPG and naphtha into hydrocarbons like ethylene, propylene, and benzene. These substances are critical for the production of various plastics across other Dow factories.
Age Balt, the EMEAI Maintenance Productivity Leader, oversees maintenance for Dow’s European locations, including Terneuzen. He tells us: “My team is multidisciplinary and handles minor disruptions as well as preventive, corrective, and project-based maintenance. We are also responsible for major maintenance events, which occur every eight years, requiring extended shutdowns of the squatters.”
To enhance efficiency, Dow partnered with Emixa to create customized training programs and train maintenance planners in optimal SAP usage. This tailored training significantly boosted the planners' efficiency and productivity, marking a crucial step towards more effective planned maintenance through advanced SAP utilization and well-trained people.
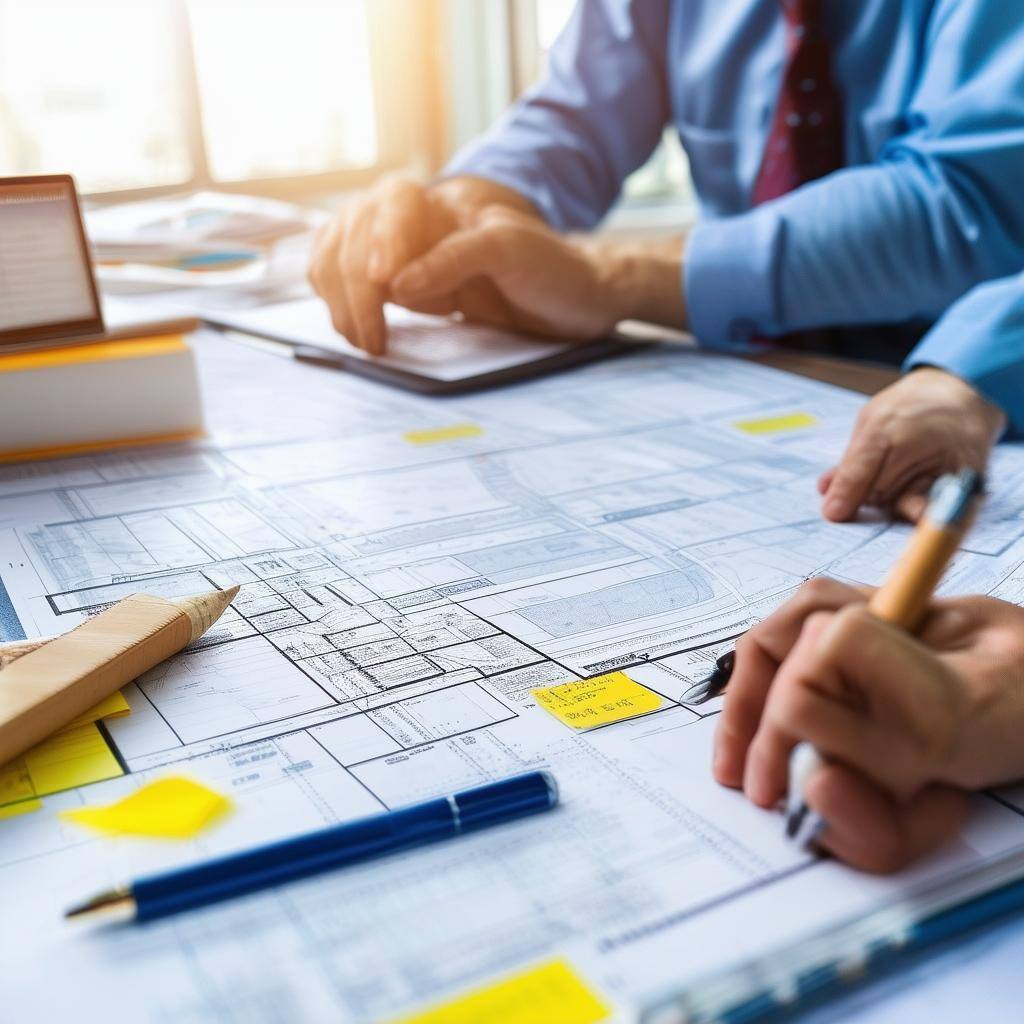
Business Challenges
Maintaining Dow's complex installations requires efficient, high-quality preparation. In the so-called 'Make Product Work Process', the scope is processed into clear work packages. These packages are in turn related to thorough planning of internal and external employees, materials, tools and equipment.
Dow's maintenance processes are supported by a suite of systems, including SAP Enterprise Asset Management (SAP EAM), Oracle Primavera for scheduling, and GE Predix APM for risk management. "SAP is essential for managing our processes and creating comprehensive work packages," says Age Balt. "However, we observed inefficiencies in system usage, with previous work packages not being reused, leading to redundant efforts Additionally, some Maintenance Group Leaders (MGLs) did not fully understand what the field planners needed to process in SAP. In turn, field planners often lacked knowledge of the production plant. This resulted in suboptimal work packages, leading to capital inefficiencies and poorly prepared job starts.”
Robson Pollitz, an MGL, noted, "After the implementation of SAP, field planners mainly learned which buttons to press, but not the rationale, missing optimization opportunities. Effective field planners must utilize SAP intelligently."
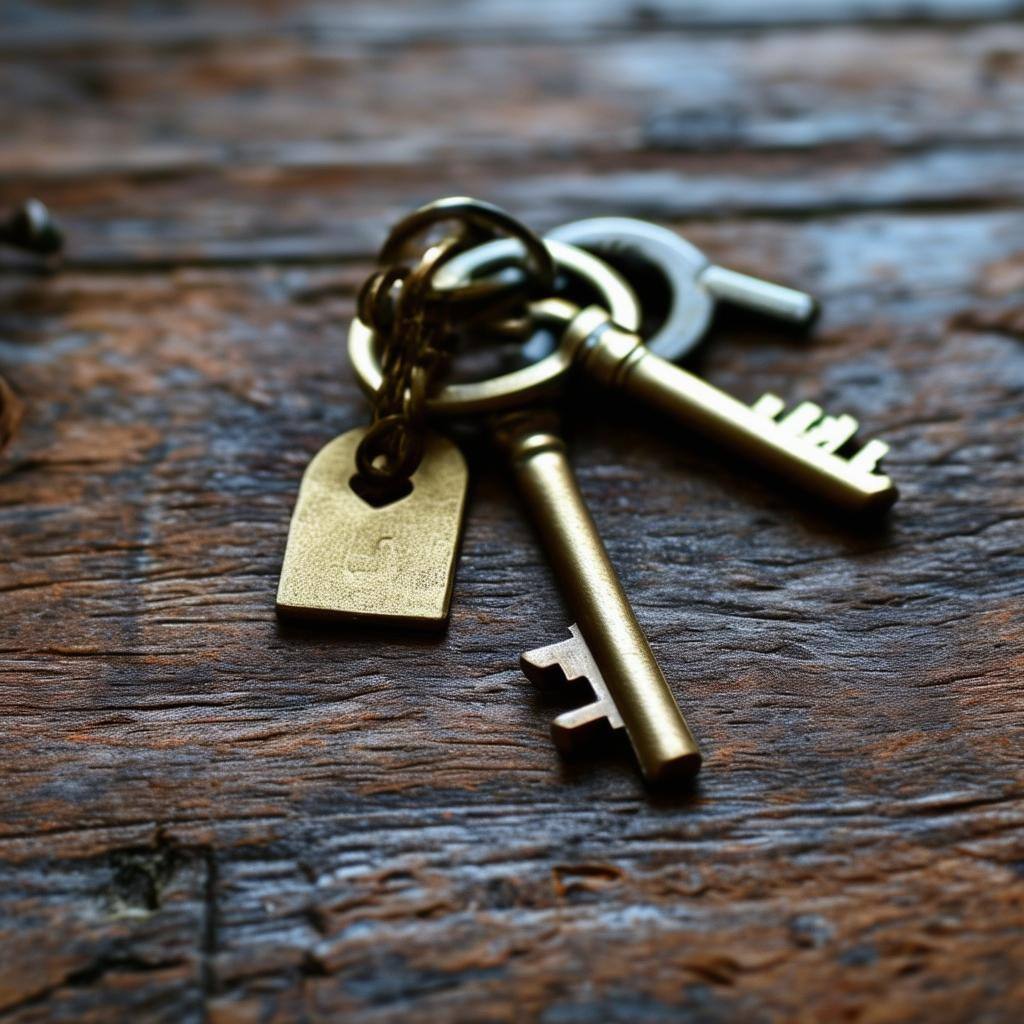
Keys to Success
Dow enlisted Emixa to develop tailor-made training programs aimed at optimizing SAP usage and enhancing the productivity of field planners to the right level.
Emixa has been involved in the project from day one, collaborating closely with Dow to form a team that includes every role in the ‘Make Product Work Process’ “After extensive investigation of the maintenance process and the associated systems via interviews, we quickly determined that Dow has a highly mature maintenance organization,” Burgemeester, an Emixa consultant noted. “However, opportunities were being missed due to inconsistent data recording. Multiple operational methods were used for the same process. Therefore, Dow needed to streamline to one way of working to ensure consistency and optimize performance.”
The team systematically explored the best practices for Dow’s field planners and how SAP could optimally support them. Burgemeester explained, “Our PowerPoint presentation gradually grew into a comprehensive document describing accurately Dow's working method. This formed the basis of a seven-day training course, including a tough exam. Next the material was refined through pilot testing and feedback.”
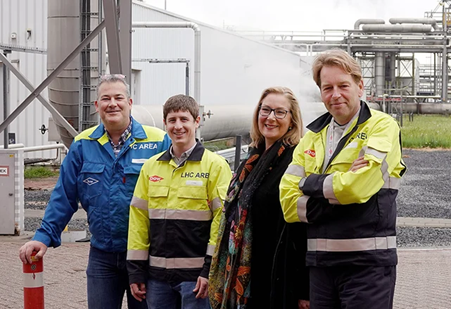
Results
While the training primarily focuses on the field planner role, the initial training days also cover the other roles in the ‘Make Product Work Process’. This ensures that everyone understands their specific role within the working method and what the consequences of any imperfections may be.
Dow’s approach, requiring all field planners to follow this training, ensures a uniform and consistent method across all plants and specializations. To date, more than 150 people have followed the training in eighteen training cycles.
Overall, the field planners became significantly more efficient and productive by reusing previously created work packages. This initiative marked an important step towards efficient planned maintenance through optimal use of SAP and well-trained people.
Explore our Portfolio
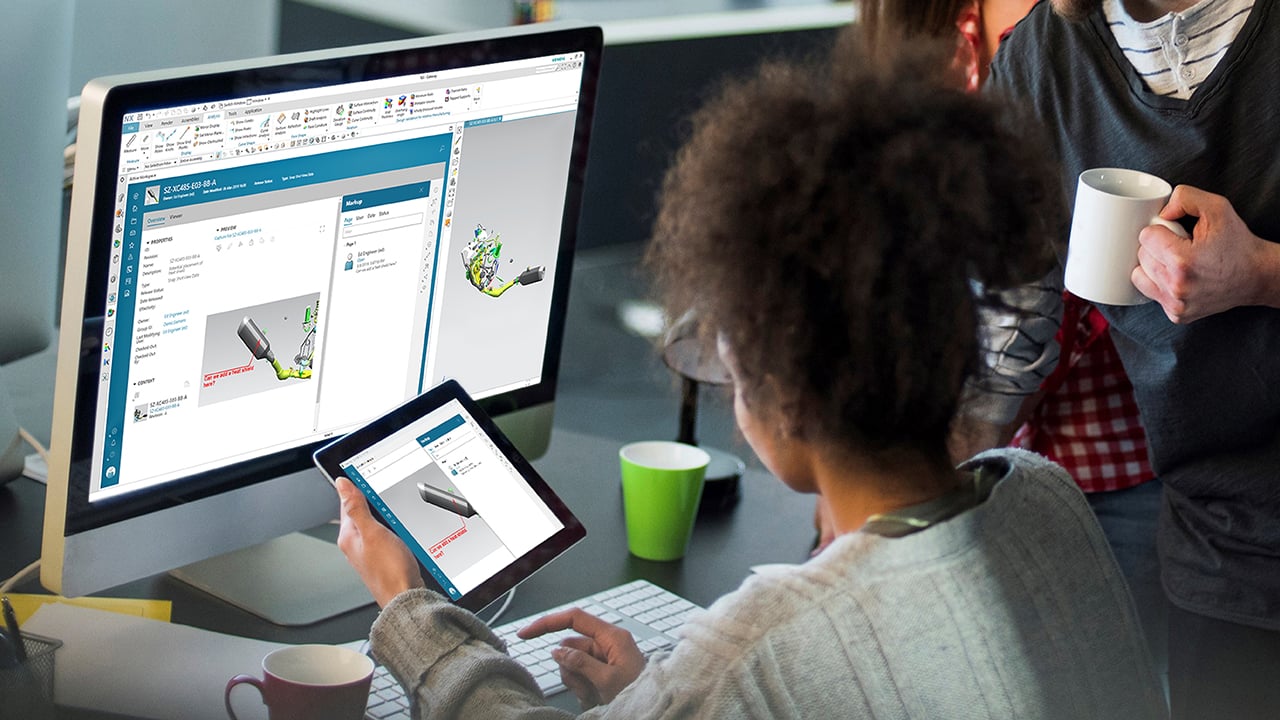
Product Lifecycle Management
Our PLM practice powers industry innovation through design, simulation, manufacturing, and effective project management in the manufacturing industry.
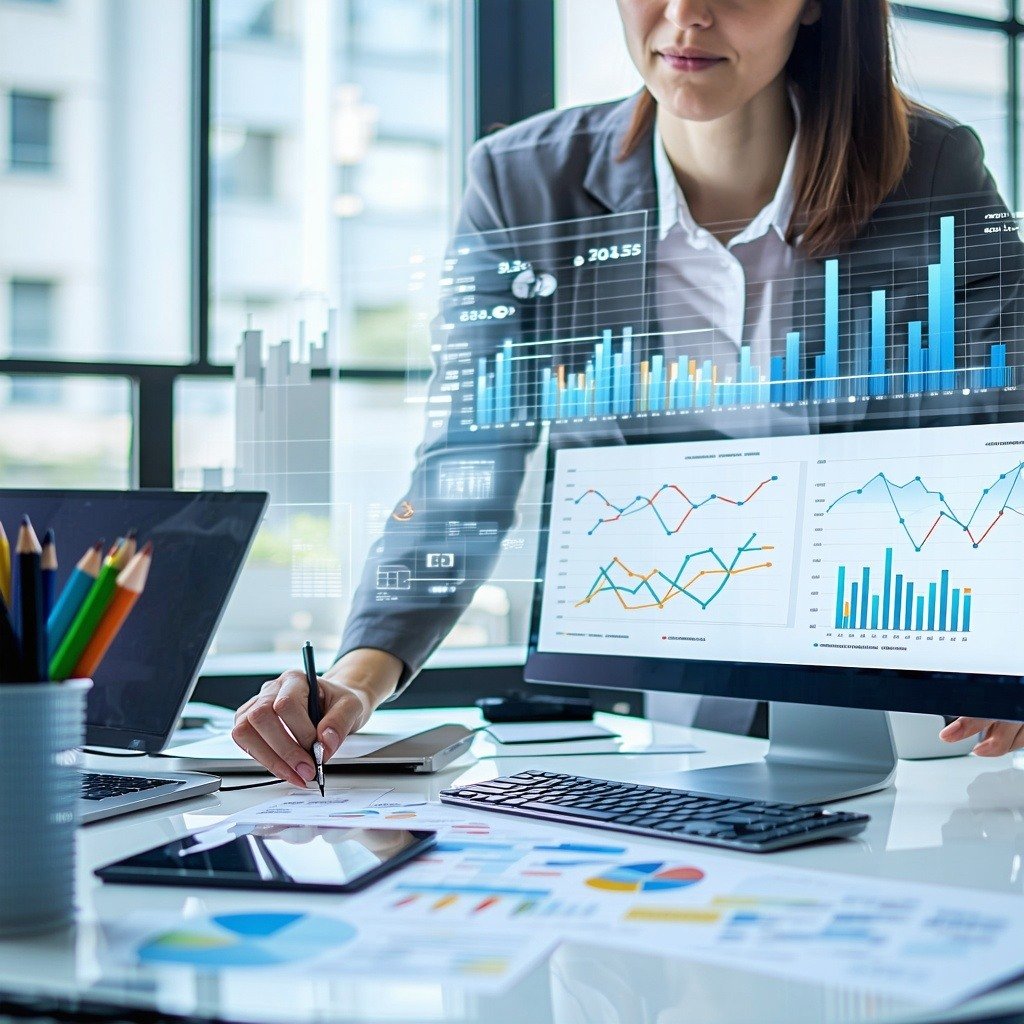
Enterprise Resource Planning
Our ERP practice leverages SAP solutions to enhance efficiency, streamline supply chains, and improve resource management in the manufacturing industry.
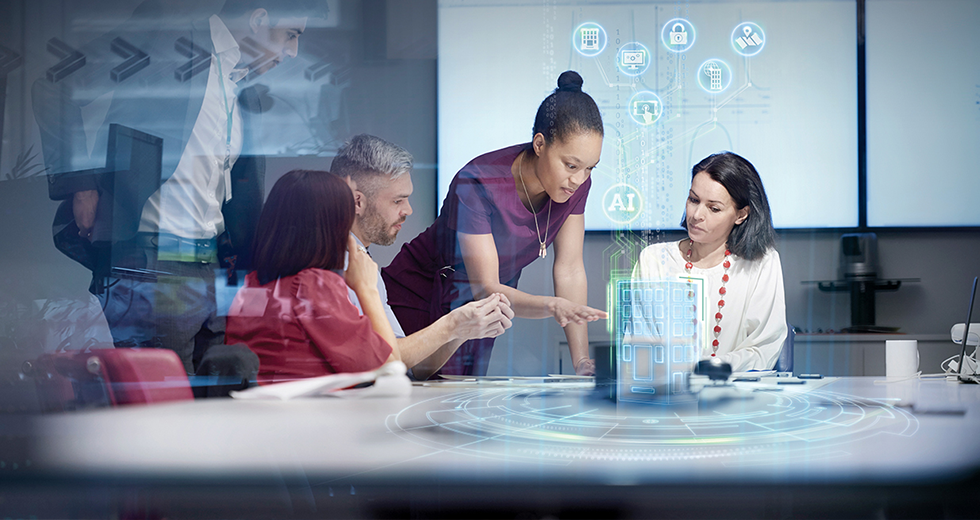
Applications
Our specialist practice for the manufacturing industry creates tailored solutions to drive innovation and streamline operations using Mendix-based applications.
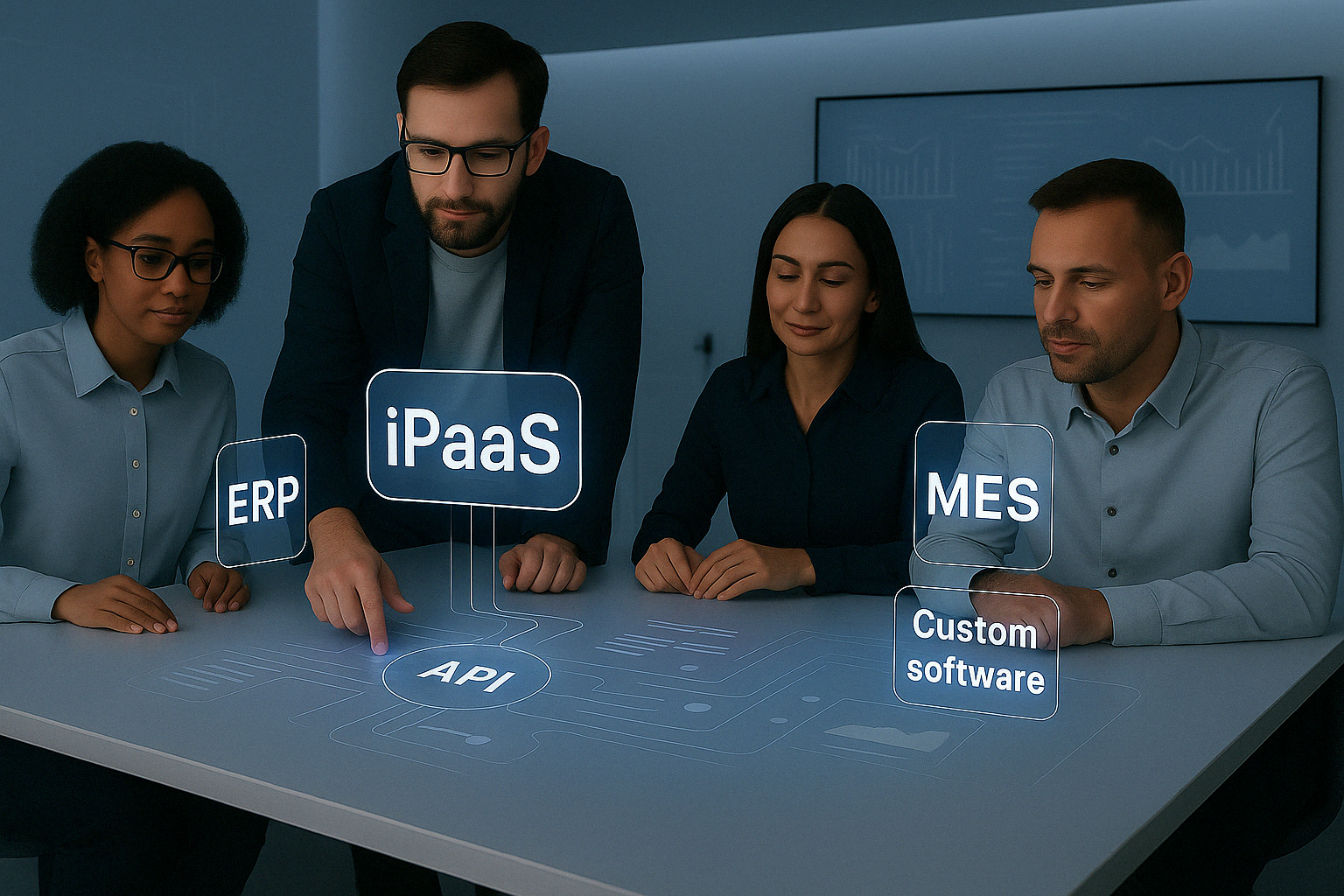
Integrations
Our specialist practice uses Boomi integrations to ensure smooth connectivity and data integration for improved operations in the manufacturing industry.
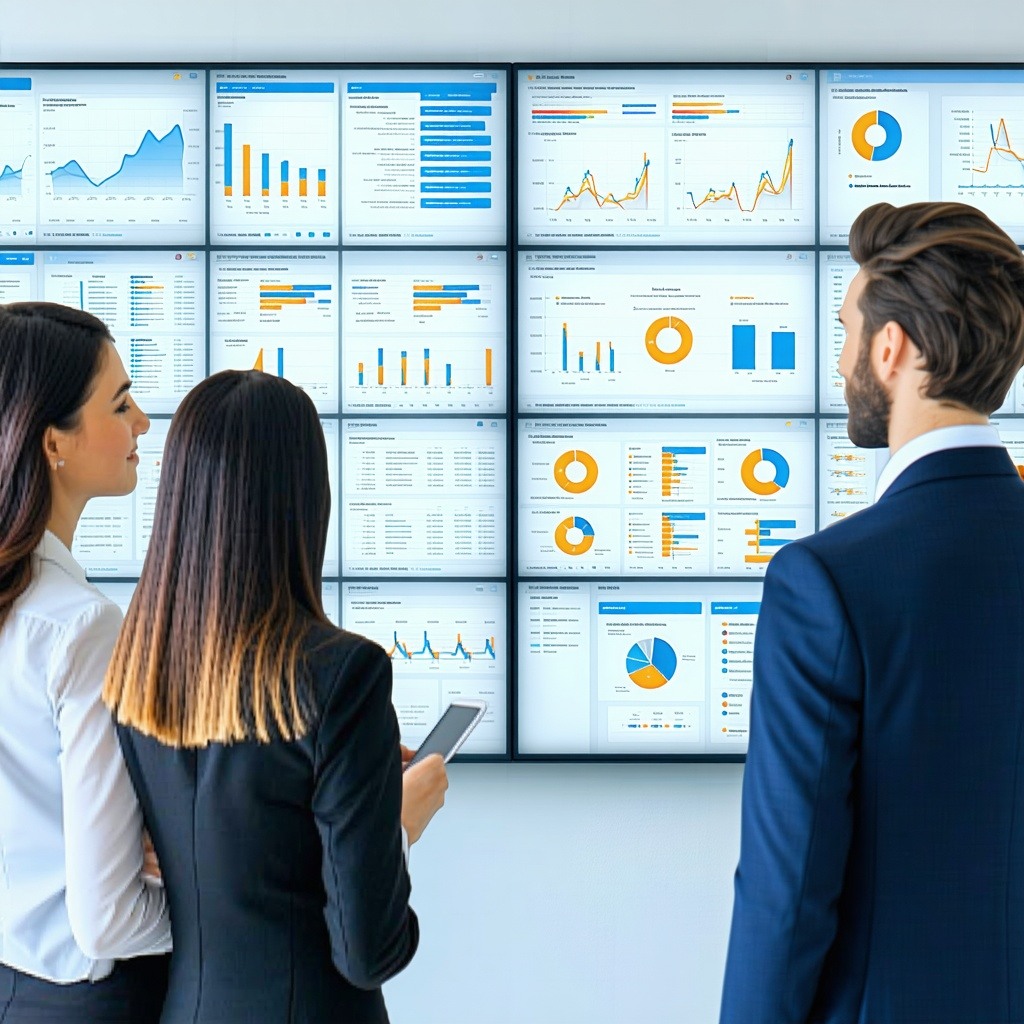
Data & Analytics
Expertise in Data Analytics tailors BI & AI strategy, data science, engineering, IoT platforms, ESG reporting, and financial analytics in the manufacturing industry.
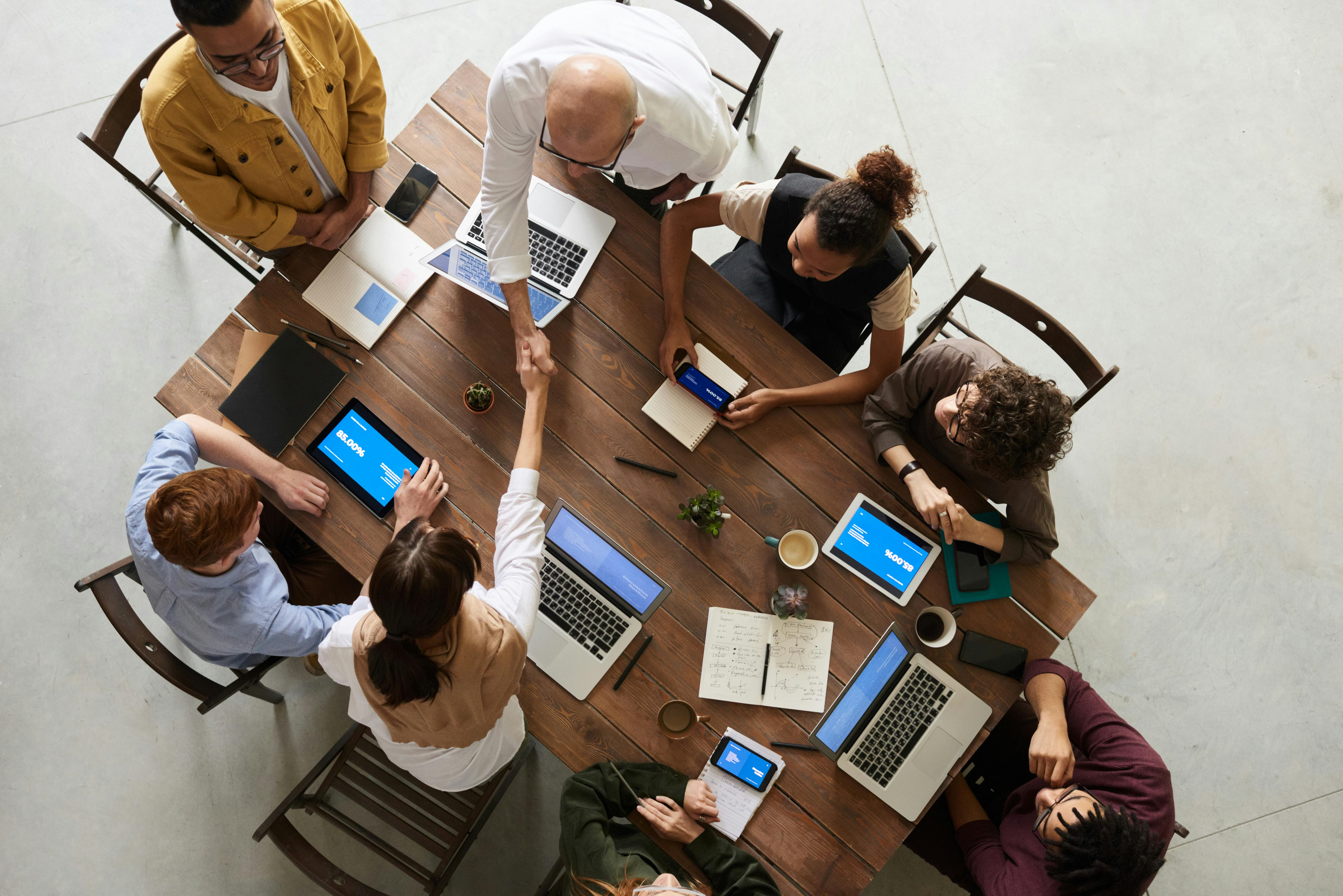
Management Consulting
Management Consulting offers strategic guidance in the manufacturing industry, fostering digital transformation and operational improvement.
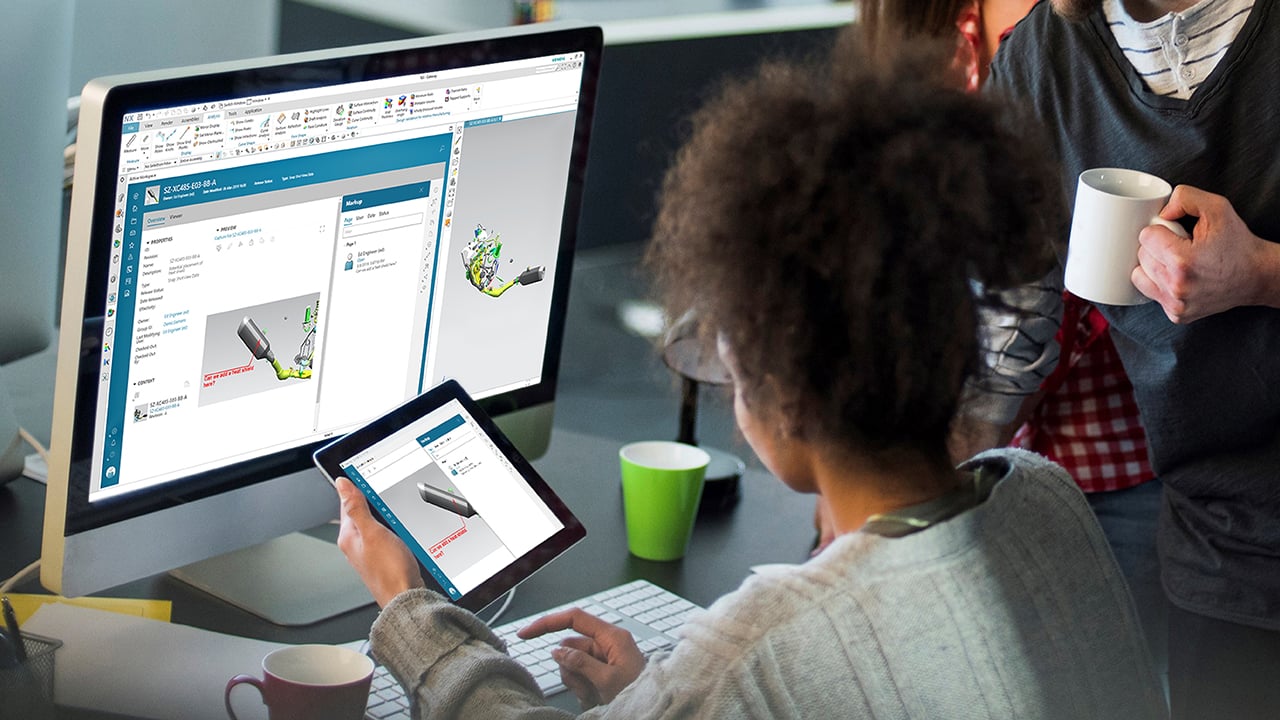
Product Lifecycle Management
Our PLM practice powers industry innovation through design, simulation, manufacturing, and effective project management in the manufacturing industry.
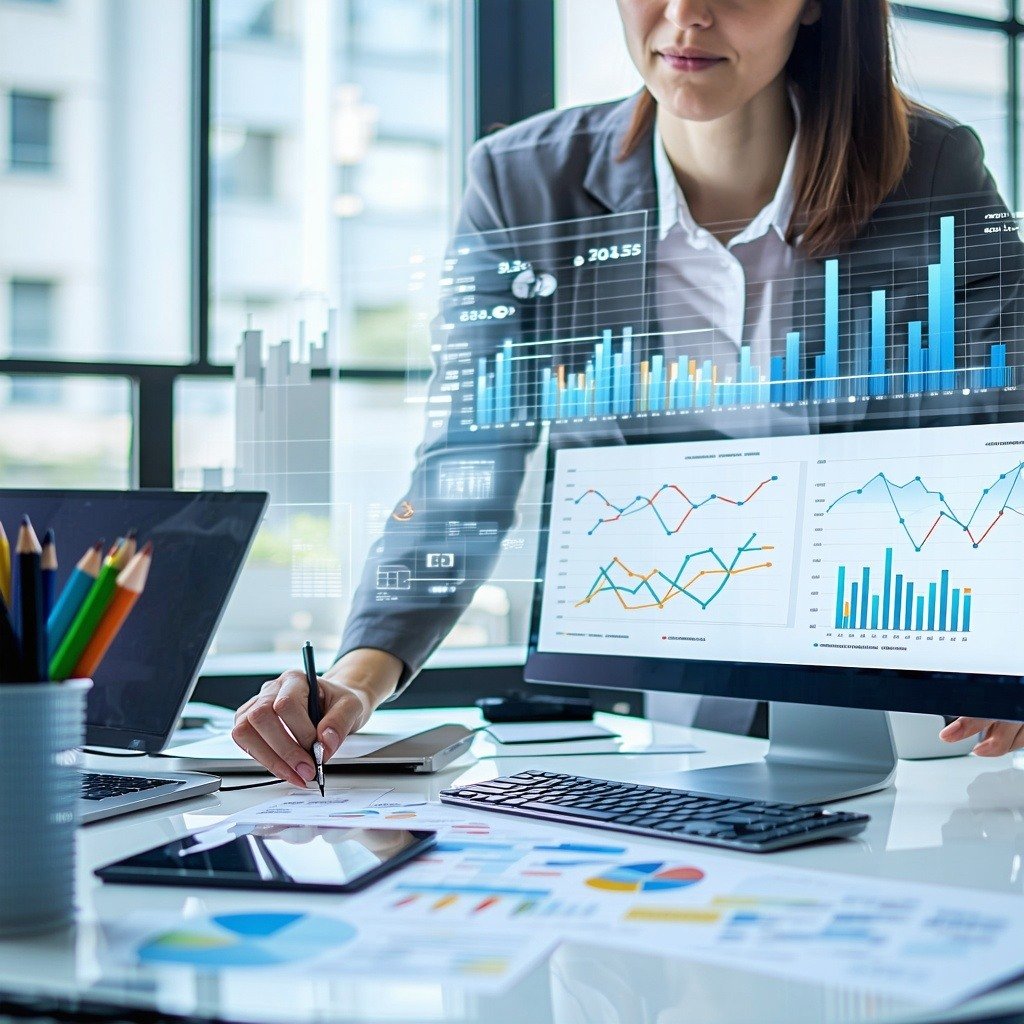
Enterprise Resource Planning
Our ERP practice leverages SAP solutions to enhance efficiency, streamline supply chains, and improve resource management in the manufacturing industry.
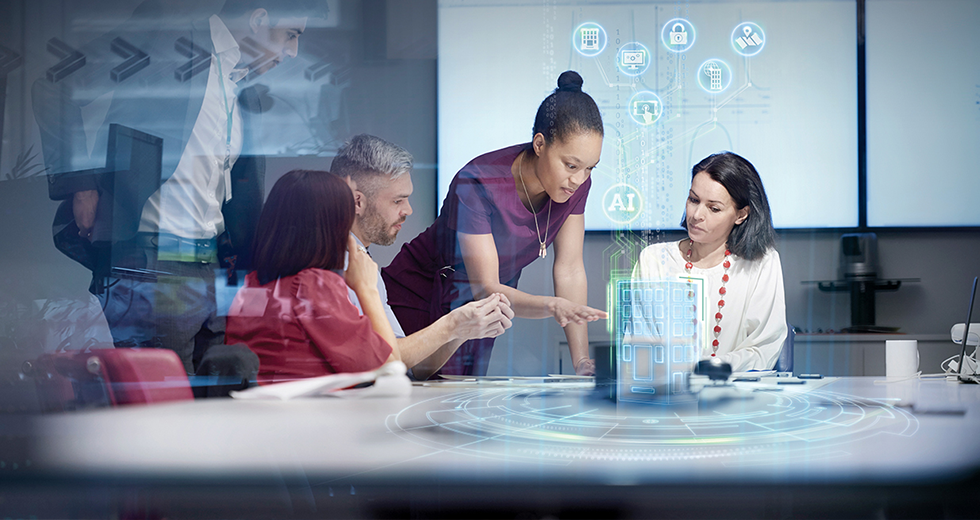
Applications
Our specialist practice for the manufacturing industry creates tailored solutions to drive innovation and streamline operations using Mendix-based applications.
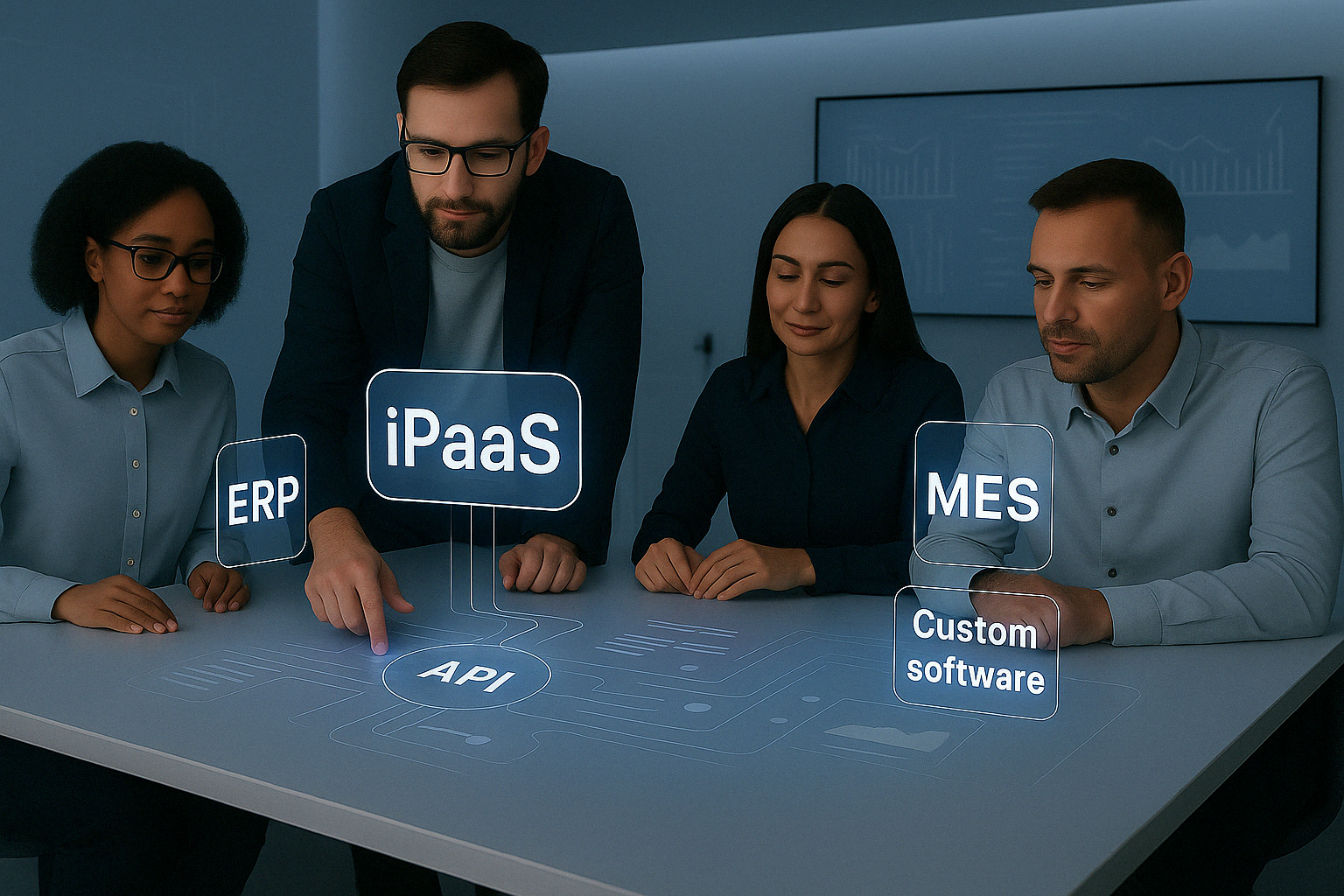
Integrations
Our specialist practice uses Boomi integrations to ensure smooth connectivity and data integration for improved operations in the manufacturing industry.