Business Challenges
- Balancing growth in tools with a constant workforce.
- Transition from an outdated system to Siemens NX™ for development.
- Striving for smarter work through IT applications and shortening lead times.
Keys to Success
- Incremental implementation of innovations with thorough evaluations.
- Testing and utilizing Siemens NX™ Design Simulation for FEM analyses.
- Utilizing Siemens Teamcenter® for simultaneous collaboration and version control.
Results
- Demonstrable value of tooling with problem avoidance and increased efficiency.
- Initial time investment in FEM analysis leads to long-term efficiency gains.
- Improved 'first-time-right-percentage' due to FEM analyses with Siemens NX™ Design Simulation.
Case study ART Group
ART Group functions as a comprehensive provider of product creation processes, covering the entire spectrum from the initial conceptualization phase to the mass production stage, and everything in between. Originating initially as a specialized toolmaker, this organization has significantly expanded its global operations and evolved into a supplier that offers end-to-end product creation solutions. Among its core competencies, ART Group develops and manufactures mass production processes, crafting essential (hard)metal tool components such as stamping dies and injection molds, all produced in-house from raw materials. These meticulously designed tools are either directly distributed to their clients or utilized in-house for production purposes across various industries, with a significant presence in markets including automotive, consumer goods, and the connector industry.
%2015%25.png?width=400&height=400&name=812x812%20Image%20(square)%2015%25.png)
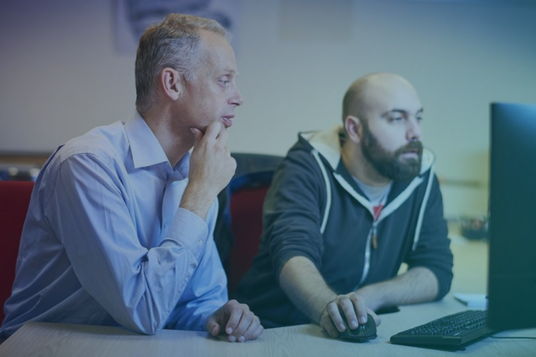
Business Challenges
"The design process of a tool is incredibly important," stated Johan Beijer, FEM Analyst at ART Group. "Which parts of the process do you execute in what sequence? And in how many steps?" Art Group tailors this process based on product and process specifications. First, we determine the requirements, then draft, fabricate, and test the tool. Around a decade ago, ART Group made the pivotal shift from an outdated system to Siemens NX™, a move that marked the beginning of its continued development journey. However, today's market landscape presents a new set of challenges. Johan elaborates, saying, "We aim to expand our tool repertoire while maintaining a relatively stable workforce. Achieving this requires employing IT to work even smarter, such as reducing lead times. I am convinced that computers can do much more for us, and in this regard, Emixa Industry Solutions can assist us."
Keys to Success
ART Group's approach to innovation is deliberate and gradual, with a strong focus on assessing the potential benefits of new tools before implementing them extensively. Because change takes time. Johan explains, "Sometimes, I hear designers discussing certain aspects and think surely there must be a faster way to do things." Cards provided a three-month test license for Siemens NX™ Design Simulation, allowing ART Group to assess its practicality and the enthusiasm of their designers. Through FEM analyses in NX™, they analyse stresses and deformations in tool components, identifying potential fracture risks. Methods like 'one-step-folding' streamline strip bending, accelerating the transition from strip setup to tool drawing. ART Group also plans to expand their toolset with complementary functionalities to further enhance efficiency.
Siemens Teamcenter® plays a crucial role in enabling multiple colleagues to work simultaneously on projects. It facilitates remote collaboration, akin to physical gatherings that promote cross-pollination of ideas. This collaborative platform serves as a technical ledger with version control, aligning with ART Group's increased emphasis on standardisation, making it an indispensable tool for their operations.
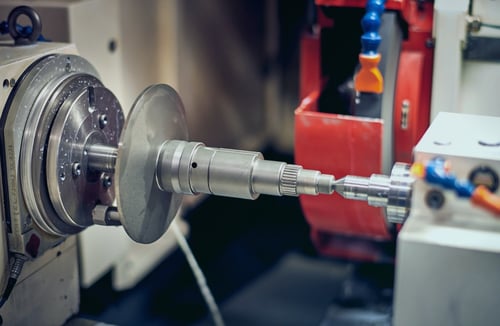
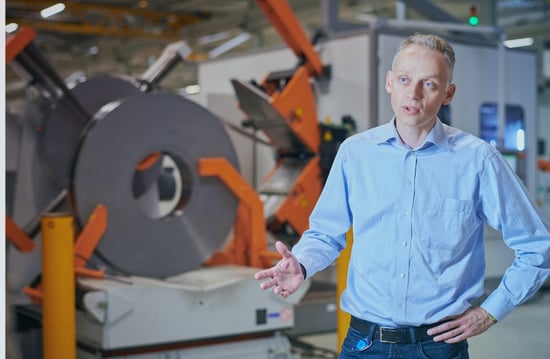
Results
The value of tooling at ART Group is beyond dispute, with a proven track record of delivering tangible benefits. Preventing even just one or two problems each year is sufficient to justify the investment. While the initial phase demands more time, with an FEM analysis taking half a day at first, it quickly becomes more efficient, reducing to just an hour or two. Although there's an upfront investment, the long-term payoff comes through enhanced automation. This transformation is clearly reflected in the remarkable increase in our first-time-right percentage. Currently, projects consistently achieve immediate success, thanks to the FEM analyses we conduct, including those using Siemens NX™ Design Simulation.