- Home
- Cases
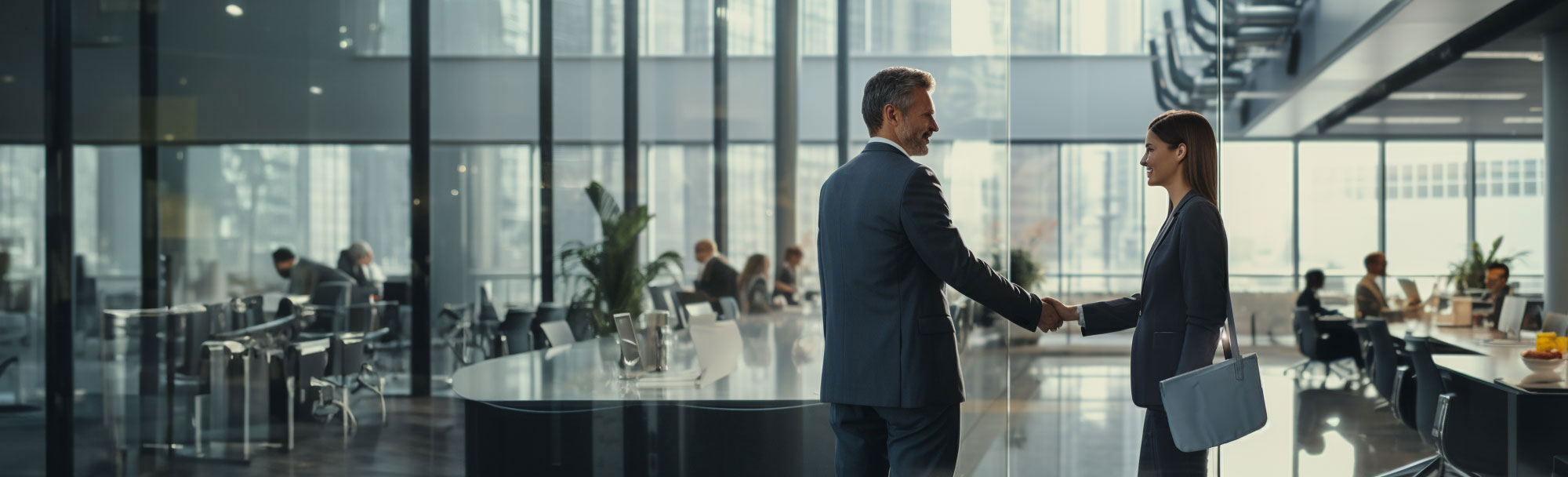
Business Challenges
- Meet the precise requirements of OEM customers
- Develop innovative designs quickly
- Work to the exacting standards required to win racecar competitions
Keys to Success
- Design team responds at the high speed demanded by the motorsports industry
- Engineers quickly establish which components will fit within a car shell
- Team uses analysis tools for easy design optimization and synchronous technology to expedite engineering changes
Results
- Everyone works on the same assembly using accurate data
- Attention to detail and tight tolerances achieved within very short timescales
- NX acts as the backbone to RML’s engineering organization
Case study RML Group
RML use their decades of experience and competitive prowess for powertrain and chassis development as well as concept vehicles and high-performance road and touring cars. Their in-house team has not only designed and developed some of the best performing race engines in the world, but also work for OEMs and specialist automotive suppliers.
The company holds an impressive number of titles for the FIA World Touring Car Championships drivers’ and manufacturers’ titles, in partnership with Chevrolet in 2010, 2011 and 2012. The motorsports industry has high demands that RML must respond to quickly, this means the team must have the design, manufacturing and simulation tools to enable them to be flexible and make amendments in short timeframes.
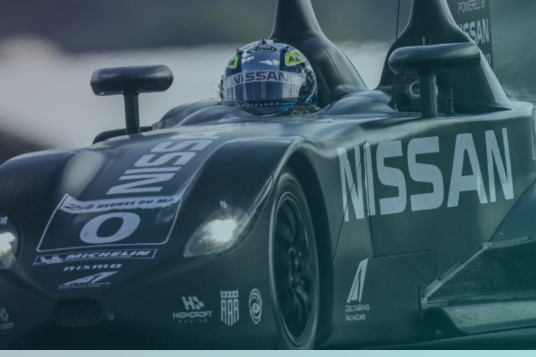

Business Challenges
RML use Siemens Digital Industries PLM software to help them stay ahead of the competition and meet consumer needs. NX is used to address its rigorous CAD, CAM and CAE needs and now acts as the backbone of the organisation.Engineers at RML are taking advantage of the vast range of tools in NX, including those that assist with clearance and geometry analysis of moving parts, such as those used in a vehicle’s suspension. NX has removed ambiguity and uncertainty when working with full car assembly models with automatic, lightweight handling and access to the correct data for everyone in the team. As a result, RML are able to reduce costly errors and design a model with a lot of detail and tight tolerances in a short period of time.
Keys to Success
Daniel Manse, senior design engineer at RML, says that the designers really appreciate NX for surfacing work and make extensive use of assemblies, in particular to assist with clearance and geometry analysis of moving parts, such as those used in a vehicle’s suspension.
“The ability to use NX for assemblies and the enhancement of assembly management tools over the years are some of the significant advantages we gain from NX. The automatic, lightweight handling of large assemblies has made a big difference to how we work. With a full car assembly on screen, everyone can comfortably work using the same data without guesswork or interpretation. There is no chance of getting lost in our own corner of the car; we see the whole picture and avoid costly errors.
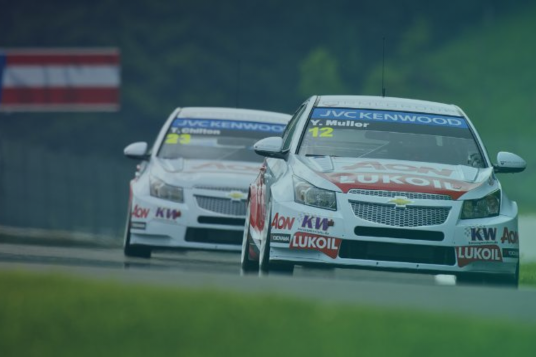
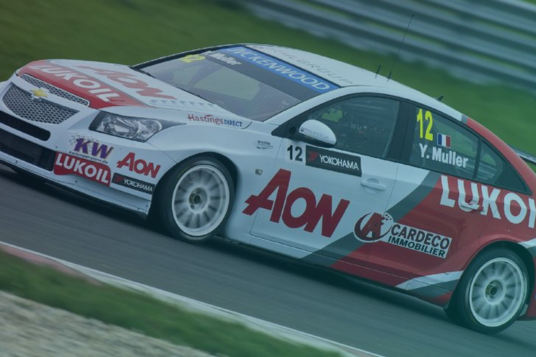
Results
”Manse points out: “One of the beauties of NX is that it has lots of tools, such as synchronous technology. We frequently use the direct modeling tools within NX to make quick changes to STEP or IGES models received from suppliers. We can, for example, move holes and bosses around very quickly. We also tend to use those tools for exporting products to CFD (computational fluid dynamics), where we need to remove the features quickly to dumb-down a model before it is sent out to specialist suppliers for CFD and FEA (finite element analysis) study.”
RML’s design team employs the CAD models created using NX to feed the production department. Manse explains that RML does quite a lot of work with sheet metal: “Creating flat patterns allows us to laser or waterjet cut the profiles. This cuts down significantly on the cost of sheet metal parts whilst increasing accuracy and reducing the need for jigs on some components. NX is completely fundamental to everything we do. We could not design a racecar without it.”